Aktualności Prom-nasos
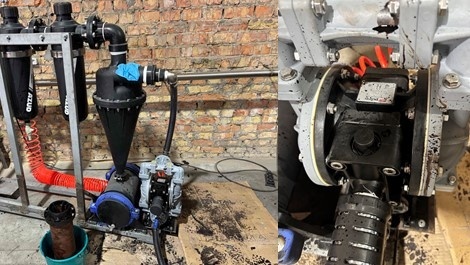
Pompy membranowe serii DP tureckiego producenta Diapump to pompy zasilane sprężonym powietrzem. Sprężone powietrze trafia do bloku rozdzielającego, który naprzemiennie kieruje ciśnienie do komór powietrznych, zmuszając membranę do ruchów posuwisto-zwrotnych, co zmienia objętość komory roboczej (produktowej) i powoduje przepompowywanie.
Pompy wykonane z tworzyw sztucznych – PP, PVDF – mogą tłoczyć dość agresywne ciecze, takie jak kwas siarkowy, azotowy, solny, mieszanki kwasów, roztwory galwaniczne itp. Dodatkowo konstrukcja pompy pozwala na tłoczenie cieczy z pewną zawartością cząstek stałych, w zależności od typu pompy.
Ciśnienie robocze pompy dla cieczy uznaje się za jednostkę niższe od ciśnienia powietrza. Maksymalne ciśnienie powietrza wynosi 7 barów, więc ciecz może być tłoczona pod ciśnieniem około 6 barów. Zaleca się jednak korzystanie z wykresu pracy pompy, dostępnego w katalogu dla każdego modelu.
Na wykresie czerwone linie przedstawiają ciśnienie powietrza, czarne krzywe – zużycie powietrza. W punktach przecięcia można odczytać uzyskane ciśnienie i wydajność cieczy w zależności od parametrów powietrza.
Nic dziwnego, że takie właściwości pomp skłaniają inżynierów i technologów do ich zastosowania w procesach filtracji.
Jednak przy stosowaniu pompy membranowej do filtracji należy dokładnie obliczyć ciśnienie i uwzględnić jej zasadę działania.
Po pierwsze – pompa membranowa działa pulsacyjnie i bez użycia specjalnych tłumików filtr będzie narażony na niewielkie uderzenia hydrauliczne przy każdym ruchu membrany, co może skrócić jego żywotność.
Po drugie – w przypadku zanieczyszczenia filtra rośnie ciśnienie w linii tłoczącej, co może doprowadzić do zatrzymania pompy.
Wniosek – stosowanie pomp membranowych w systemach filtracyjnych jest możliwe i skuteczne, pod warunkiem odpowiedniego doboru i obliczenia parametrów, szczególnie tam, gdzie użycie innych pomp jest utrudnione lub niemożliwe. W innych przypadkach należy rozważyć zastosowanie chemicznych pomp wirowych, pomp z sprzęgłem magnetycznym lub pomp wirowych ze stali nierdzewnej.
13 lipiec 2025
Wybór średnic rur podłączanych do pompy
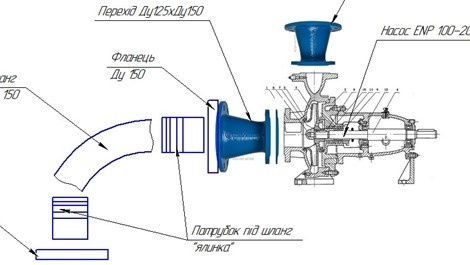
Głównymi parametrami praktycznie każdej pompy są bez wątpienia wydajność objętościowa (w metrach sześciennych na godzinę, litrach na minutę, galonach na minutę itp.) oraz ciśnienie, jakie wytwarza (lub podciśnienie, jeśli to pompa próżniowa).
Oczywiście producent dostarcza dane techniczne pompy i gwarantuje, że może ona zapewnić podane parametry. Parametry te są zawarte w katalogach, broszurach technicznych producenta, a także na tabliczce znamionowej konkretnej pompy.
Poza informacjami o parametrach hydraulicznych (maksymalna wydajność, maksymalne ciśnienie lub parametry znamionowe), na tabliczce znamionowej znajduje się również moc silnika elektrycznego i jego parametry.
Jednak często pomijane są średnice króćców, czyli średnice przyłączeniowe pompy do systemu, w którym pracuje (po angielsku „Inlet” i „Outlet”).
Na pierwszy rzut oka wszystko wydaje się proste – jeśli na pompie podano określone średnice przyłączy, to właśnie takie rury należy zastosować. W rzeczywistości to pozornie logiczne założenie jest błędne i może prowadzić do wielu problemów podczas eksploatacji systemu nawadniania, cyrkulacji lub wodociągu.
Trzeba zrozumieć, że średnice rur podłączanych do pompy powinny być dobrane na podstawie obliczeń hydraulicznych. Jest to jedyny poprawny sposób doboru średnic rurociągów. Często pompę kupuje się jako zamiennik i jeśli jej parametry nie są gorsze od poprzedniej, problemy raczej się nie pojawią. Jednak jeśli pompa ma pracować w nowym systemie, należy wykonać obliczenia hydrauliczne.
Ważne jest, aby pamiętać, że pompa to urządzenie o działaniu dynamicznym, a to, że króciec tłoczny pompy ma średnicę np. DN50, nie oznacza, że rura tłoczna również powinna mieć DN50.
Warto także wiedzieć, że parametry podane przez producenta w dokumentacji technicznej odnoszą się do konkretnych warunków. Dla pomp odśrodkowych konsolowych dane na tabliczce znamionowej podawane są przy następujących warunkach:
temperatura wody 20˚C;
głębokość zasysania 1,5 m;
gęstość cieczy 1000 kg/m³.
W rzeczywistych warunkach wszystkie powyższe parametry zwykle się różnią. Szczególne znaczenie dla pomp odśrodkowych ma średnica rury ssącej. Aby pompa się nie „dusiła”, nie zasysała powietrza i wytwarzała wymagane ciśnienie, średnica rury ssącej powinna być zawsze większa niż średnica króćca ssącego pompy.
Przykład zależności średnic pompy i rury ssącej przedstawiony w katalogu jednego z europejskich producentów:
Jak pokazano w tabeli, średnica rurociągu ssącego powinna być większa, aby nie zakłócać normalnego dopływu cieczy do komory roboczej pompy. Jest to szczególnie istotne, gdy pobór wody następuje z głębokości 4 metrów lub więcej. Przy zwiększonej głębokości zasysania należy uwzględnić, że charakterystyka przepływowo-ciśnieniowa pompy się zmienia (obserwuje się spadek wydajności i ciśnienia).
Na poniższym rysunku przedstawiono typowy przykład podłączenia pompy do systemu nawadniania kropelkowego, która pobiera wodę z rzeki poniżej poziomu instalacji pompy.
Różnica wysokości między lustrem wody a osią pompy nie jest duża – tylko 1,5–2 m, ale długość rury ssącej wynosi około 5 m, dlatego pompę z króćcem ssącym DN125 należy podłączyć rurą o większej średnicy – co najmniej DN150.
11 lipiec 2025
Kontrola przepływu pompy wyporowej
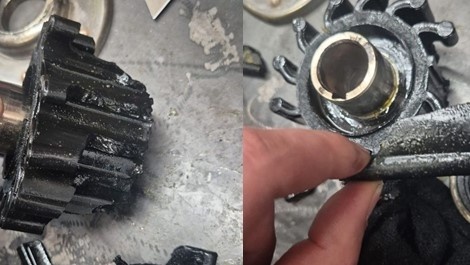
Pompy wyporowe to urządzenia, które działają na zasadzie zmiany objętości komory roboczej. Może się to odbywać dzięki ekscentrycznie zamontowanemu wirnikowi (w pompie wirnikowej ), obrotowi zębatek , ruchowi tłoka, ruchowi membrany , zmianie objętości węża ( pompa perystaltyczna ) itd.
Ze względu na zasadę działania takiej pompy można wywnioskować, że regulowanie jej wydajności za pomocą armatury odcinającej (poprzez zamykanie zaworów na linii tłocznej lub ssącej) może być szkodliwe i niebezpieczne zarówno dla pompy, jak i systemu, w którym pracuje.
W przeciwieństwie do pomp dynamicznych, te pompy nie wytwarzają ciśnienia, lecz są w stanie pokonać określone ciśnienie, które może wynosić dziesiątki, a nawet setki megapaskali (MPa).
Oznacza to, że jeśli na przykład pompa zębata pracuje w układzie cyrkulacyjnym, manometr będzie wskazywał opór systemu rurociągów (rury, kolana, filtry).
Manometr w układzie chłodzenia transformatora. Pracuje pompa zębata ENP 1010 z maksymalnym ciśnieniem 15 bar. Manometr wskazuje 0,2 bara.
Poniżej na zdjęciu – efekt zamknięcia zaworu na rurze tłocznej w tym samym systemie.
W wyniku zamknięcia zaworu doszło do uszkodzenia uszczelki.
Kolejny przykład – próba regulacji przepływu za pomocą zaworu w pompie wirnikowej AlphaDynamic .
W rezultacie – uszkodzenie wirnika i konieczność naprawy.
Wniosek – pracę pompy wyporowej należy regulować za pomocą obejścia lub falownika. KATEGORYCZNIE ZABRANIA SIĘ zamykania armatury odcinającej na wejściu i wyjściu z pompy. Jeśli w systemie nie ma zainstalowanego obejścia, obowiązkowo muszą być zamontowane zawory bezpieczeństwa.
03 lipiec 2025
Specyfika działania pomp z mokrym wirnikiem
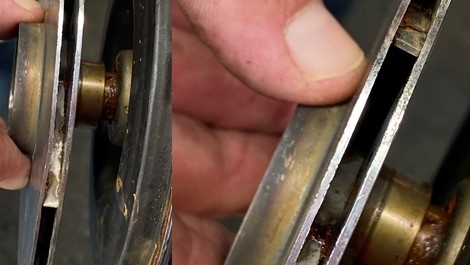
Pompy z „mokrym wirnikiem” to duża grupa pomp, które znajdują szerokie zastosowanie w systemach ogrzewania i chłodzenia.
Dzięki cichej pracy, niskiemu zużyciu energii oraz braku uszczelnienia czołowego, zajmują one wyjątkowo szeroką niszę zarówno w systemach przemysłowych, jak i domowych instalacjach grzewczych.
Obecnie można kupić zarówno najprostsze wersje — pompy jednotypowe bez sterowania, jak i „inteligentne” pompy smart z elektronicznym sterowaniem, możliwością kontroli ciśnienia i przepływu oraz wyborem różnych trybów pracy.
Mimo wszystkich powyższych zalet, pompy te mają jedną istotną wadę – jakość wody lub czynnika grzewczego, z którym pracują. Niezależnie od obecności nowoczesnej elektroniki, podstawowym elementem tego typu urządzenia pozostaje część mechaniczna – „mokry wirnik”.
Ponieważ wirnik jest omywany przez pompowane medium, jego jakość musi być odpowiednia – czysta, bez zanieczyszczeń mechanicznych (zgorzelina, piasek, kamień kotłowy itp.).
Na zdjęciu poniżej można zobaczyć pompę, która trafiła do nas na serwis z powodu zablokowania wirnika po 1,5 miesiąca pracy.
Koło robocze i szczelina między wirnikiem a stojanem były zatkane zgorzeliną, co spowodowało zablokowanie wirnika.
Wniosek – aby prawidłowo korzystać z pomp tego typu, należy odpowiedzialnie podejść do uzdatniania wody. Wtedy pompa będzie działać nie tylko przez okres gwarancyjny, ale również przez wiele kolejnych lat.
W przeciwnym razie warto rozważyć zastosowanie urządzeń pompowych mniej wrażliwych na jakość wody – inline pompy z „suchym wirnikiem” , które są wyposażone w standardowy silnik asynchroniczny oraz uszczelnienie czołowe.
17 czerwiec 2025
Pompowanie dwutlenku węgla za pomocą pompy wielostopniowej
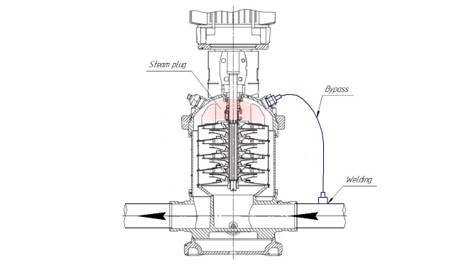
Dwutlenek węgla (CO₂) – bezbarwny gaz (w normalnych warunkach), łatwo rozpuszczalny w wodzie.
Oprócz powszechnie znanego faktu, że jest ważnym elementem procesu fotosyntezy, substancja ta jest szeroko stosowana w przemyśle spożywczym, farmaceutycznym, rolnictwie, inżynierii mechanicznej itp.
W procesie technologicznym produkcji dwutlenku węgla niezbędne są środki transportu produktu, a mianowicie agregat pompy. Dwutlenek węgla znajduje się w stanie ciekłym w niskiej temperaturze i pod wysokim ciśnieniem.
Na poniższym zdjęciu – pionowa pompa wielostopniowa zainstalowana w linii technologicznej produkcji dwutlenku węgla. Na powierzchni pompy i armatury odcinającej widoczna jest szron (zamrożona para wodna zawarta w powietrzu).
Charakterystyczną cechą tego typu pomp jest możliwość wytwarzania wysokiego ciśnienia dzięki liczbie kół roboczych umieszczonych na jednym wale jedno za drugim. Taka konstrukcja pozwala osiągać znaczne ciśnienia (od 3 do 25 bar).
Wadą pionowej konfiguracji jest niebezpieczeństwo powstawania parowo-powietrznych „zatorów” w górnej części pompy z powodu wysokiej prędkości cieczy i w konsekwencji lokalnego wrzenia dwutlenku węgla.
W tej części pompy znajduje się uszczelnienie czołowe. Element ten zapobiega wyciekom cieczy z komory roboczej i powinien być chłodzony cieczą przepompowywaną, ale ponieważ powstaje strefa parowo-powietrzna, w której uszczelnienie działa bez cieczy – „suchy bieg”, trwałość uszczelnienia czołowego znacznie się zmniejsza.
W przypadku „suchego biegu” następuje szybkie ścieranie par ciernych i topnienie pierścieni gumowych.
Aby wyeliminować ten problem, można zastosować rurkę bypassową (bypass). Element ten obwodowy pompy umożliwia odprowadzenie par do linii ssącej i tym samym zapobiega powstawaniu parowo-powietrznego „worka” w strefie uszczelnienia czołowego.
16 czerwiec 2025
Ręczne pompy beczkowe
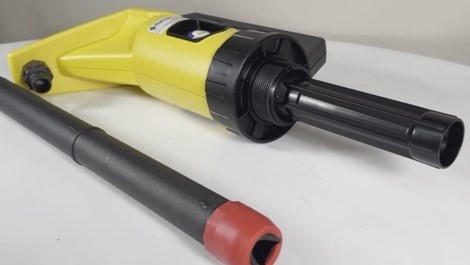
Ręczne pompy beczkowe to optymalne rozwiązanie dla małych przedsiębiorstw, stacji obsługi pojazdów, zakładów przemysłu spożywczego – wszędzie tam, gdzie zachodzi potrzeba dozowania produktu lub poboru niewielkiej ilości cieczy do konkretnego procesu technologicznego.
Pompy te mogą być wykorzystywane do rozlewu z dużych pojemników oleju samochodowego, olejów roślinnych, nawozów, preparatów enzymatycznych, środków ochrony roślin, płynów niezamarzających, glikolu, alkoholu, oleju napędowego, benzyny i innych substancji.
Nasza linia ręcznych pomp beczkowych obejmuje urządzenia włoskiego producenta FLUIMAC.
„Żółta” pompa, model N-04, przeznaczona jest do pracy z materiałami paliwowo-smarowymi oraz produktami tłuszczowymi.
Konstrukcja pompy jest prosta i niezawodna. Wysuwany pręt pozwala na stosowanie pompy w zbiornikach o różnej głębokości, a uszczelnienie z gumy FKM zapewnia odporność chemiczną i długą żywotność.
„Niebieska” pompa, model N-04 Blue, ma podobną konstrukcję, ale zastosowano w niej inny rodzaj uszczelnienia – gumę PTE, co umożliwia jej wykorzystanie do dozowania roztworów kwasów, octu, kwasu adypinowego i innych substancji chemicznie agresywnych.
Wydajność pompy przy jednym ruchu dźwignią wynosi 0,3 l, przyłącze ¾ cala.
Teleskopowa rura ssąca regulowana jest w zakresie od 500 do 950 mm i ma średnicę 34 mm.
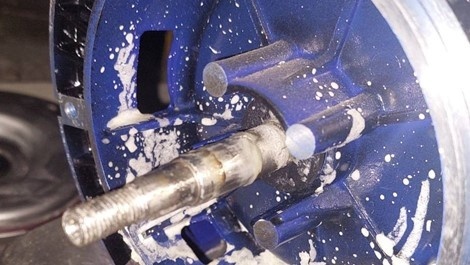
Ogólnie do produktów o wysokiej lepkości zazwyczaj stosuje się takie typy pomp jak pompy z wirnikiem elastycznym , pompy krzywkowe , zębate , membranowe , czyli głównie pompy wyporowe.
Dla niektórych produktów, takich jak olej, olej transformatorowy, mieszanka wody i mąki w proporcji 1 do 4, brzeczka piwna, zacier i podobne ciecze można z powodzeniem stosować pompy odśrodkowe z otwartym lub szerokim wirnikiem.
Ważnym elementem eksploatacji takiej pompy z wymienionymi produktami jest konieczność przepłukania części roboczej pompy po zakończeniu procesu tłoczenia.
Ten rodzaj urządzenia pompowego jest wyposażony w uszczelnienie mechaniczne , które zazwyczaj nie wymaga obsługi w trakcie pracy, jednak jeśli pompowany produkt ma tendencję do krystalizacji, przylegania lub tworzenia grudek – może dojść do uszkodzenia uszczelnienia.
Na zdjęciu poniżej widać uszkodzenie gumowego mieszka uszczelnienia mechanicznego.
Stało się to z powodu nieprzeprowadzenia na czas płukania komory roboczej pompy. W wyniku tego pary trące „skleiły się” mieszaniną skrobi i przy kolejnym uruchomieniu pompy nastąpiło zerwanie gumowego mieszka.
W konsekwencji produkt zaczął wyciekać z komory roboczej do przestrzeni między wspornikiem a silnikiem elektrycznym.
W tym przypadku operator w porę zauważył wyciek i uszczelnienie mechaniczne zostało wymienione. W przeciwnym razie długotrwały wyciek produktu mógłby doprowadzić do uszkodzenia silnika elektrycznego, co oznaczałoby znacznie wyższe koszty naprawy i opóźnienia w procesie technologicznym.
Nasza firma zajmuje się nie tylko sprzedażą urządzeń pompowych i części zamiennych do nich, ale także oferuje profesjonalny dobór i zalecenia dotyczące eksploatacji.
10 czerwiec 2025
Zalety i wady pomp z mokrym wirnikiem
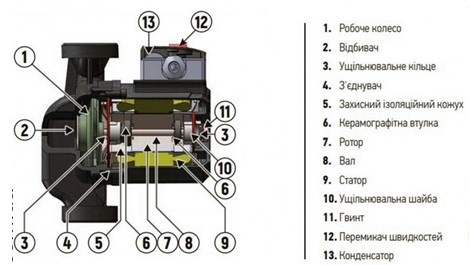
Pompy z „mokrym wirnikiem” otrzymały swoją nazwę dzięki specyfice konstrukcji – wirnik pompy jest podtrzymywany przez łożyska ślizgowe i całkowicie zanurzony w wodzie.
Główną zaletą tej konstrukcji jest bezgłośna praca. Ponieważ wirnik obraca się na łożyskach ślizgowych i nie ma wentylatora chłodzącego, pompa działa bardzo cicho. Czasami obrót wirnika można zarejestrować tylko za pomocą wskaźnika magnetycznego.
Do zalet tej konstrukcji należy również brak uszczelnień. Jest to praktycznie hermetyczna pompa, która ma tylko korek odpowietrzający na końcu.
Ponadto większość pomp z „mokrym wirnikiem” jest wyposażona w przełącznik prędkości obrotowej wirnika, co pozwala optymalnie dopasować pompę do systemu grzewczego nawet przy niewielkich błędach w obliczeniach.
Bez wątpienia w prywatnych systemach grzewczych, a także w węzłach cieplnych budynków wielomieszkaniowych, gdzie poziom hałasu jest bardzo ważnym wskaźnikiem, te pompy są praktycznie bezalternatywne.
Jednak w przemysłowych systemach grzewczych, kotłowniach, zakładach suszenia drewna, obiegowych systemach chłodzenia w przemyśle spożywczym ta konstrukcja ujawnia swoje „minusy”.
Ponieważ szczelina między wirnikiem a stojanem jest bardzo mała (0,5–2 mm w zależności od modelu), wymagania dotyczące czystości wody są bardzo wysokie. Drobiny rdzy, brudu, resztki uszczelek lub kawałki elektrody po naprawie rury czy wymianie zaworu prowadzą do awarii pompy.
Ten typ pomp ma niski poziom naprawialności. Zazwyczaj serwisanci nie wykonują oddzielnie naprawy wirnika czy stojana ani wymiany łożysk ceramicznych. Centrum serwisowe oferuje wymianę całej części pompy, której koszt stanowi około 80% ceny całej pompy.
Kolejną istotną wadą, szczególnie dla pomp przemysłowych, jest cena. Wielu światowych liderów sprzętu pompowego, takich jak Wilo, Grundfos, DAB, wycofało z produkcji modele z mechanicznym przełączaniem prędkości i zamiast tego oferuje podobne modele z regulacją częstotliwości, które czasami są droższe nawet dwukrotnie od „starych” modeli.
Alternatywnym rozwiązaniem dla zastąpienia pomp europejskich, które już nie są produkowane, mogą być jednoobiegowe pompy z „mokrym wirnikiem” EDWIN lub zastosowanie pompy inline z „suchym wirnikiem” z tradycyjnym silnikiem asynchronicznym.
06 czerwiec 2025
Zakup paneli słonecznych
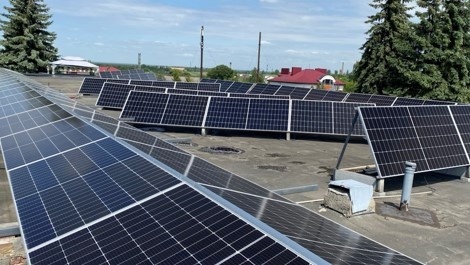
Pierwsze prototypy paneli słonecznych zostały wynalezione już w połowie XIX wieku. Następnie były udoskonalane i zyskiwały na popularności, ale dopiero w ciągu ostatnich ośmiu lat osiągnęły ogromne rozpowszechnienie. Obecnie energia słoneczna to nie tylko opłacalna inwestycja, ale także ekologiczne rozwiązanie problemów środowiskowych. Dzięki panelom słonecznym zmniejsza się emisja CO2 do atmosfery, co ogranicza ryzyko globalnego ocieplenia i zmian klimatu.
Przed zakupem paneli słonecznych należy określić, w jakim celu będą wykorzystywane: sprzedaż czy zużycie własne. Na przykład, jeśli system ma służyć osobie fizycznej do zysku, moc instalacji nie może przekraczać 30 kW. Jeśli ma służyć do zasilania domu, system dobiera się w zależności od zużycia.
Same panele różnią się mocą i materiałem wykonania: monokrystaliczne (najczęściej spotykane) i amorficzne.
Załóżmy, że potrzebujesz systemu o mocy 10 kW i wybierasz panele o mocy 560 W.
Dzielimy całkowitą moc systemu przez moc jednego panelu.
Dodajemy 15–20% rezerwy na możliwe straty.
10 000 W / 560 W = 17,8 paneli
Dodajemy 15–20%: 17,8 * 1,15 = 20,47 → zaokrąglamy do 21 paneli.
Aby uzyskać system o mocy 10 kW, należy zainstalować 21 paneli słonecznych.
Takie panele możesz kupić u nas, klikając w ten link .
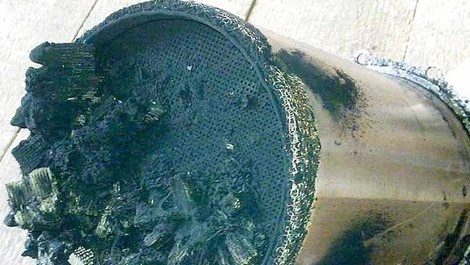
Filtry cząstek stałych (DPF) to jeden z głównych elementów układu wydechowego samochodu. Urządzenie to służy do oczyszczania gazów wylotowych silnika spalinowego z cząstek stałych powstających podczas spalania paliwa – sadzy.
Nowoczesne silniki samochodowe są wyposażone w automatykę do automatycznej regeneracji filtra, która odbywa się bez udziału kierowcy. Jednak z czasem taka regeneracja przestaje być skuteczna i konieczne jest zdemontowanie filtra w celu jego oczyszczenia na specjalnych urządzeniach.
Istnieją dwie podstawowe metody czyszczenia filtra cząstek stałych – chemiczna i hydrodynamiczna . Metoda chemiczna wymaga użycia specjalnych reagentów i odpowiedniego sprzętu.
Dla porównania, metoda hydrodynamiczna jest tańsza i bardziej ekologiczna. Pozwala na przywrócenie sprawności filtra do 98%.
Głównym elementem urządzenia do hydrodynamicznego czyszczenia jest pompa odśrodkowa . W zależności od typu filtra do jego czyszczenia stosuje się pompy o wydajności od 50 do 150 l/min i ciśnieniu 4–7 barów.
Urządzenie może być typu cyrkulacyjnego lub przepływowego . W układach cyrkulacyjnych (czyli gdy brudna woda jest filtrowana i ponownie kierowana do płukania) zaleca się stosowanie pomp jedno- lub dwustopniowych o ciśnieniu 4–5 barów.
Pompy te mają na tyle szerokie wirniki, że cząstki sadzy i zabrudzeń ich nie zatykają.
W układach przepływowych można zastosować pionowe pompy wielostopniowe wysokiego ciśnienia (5–7 barów). Woda płucząca nie trafia ponownie do pompy, lecz spływa do kanalizacji, dzięki czemu nie dochodzi do zanieczyszczenia części przepływowej.
Nasi specjaliści są zawsze gotowi pomóc w doborze sprzętu pompowego do zestawów czyszczenia filtrów DPF.