Nachrichten Prom-nasos
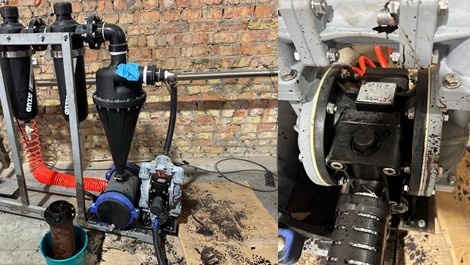
Membranpumpen der Serie DP des türkischen Herstellers Diapump sind Pumpen, die mit Druckluft betrieben werden. Die Druckluft gelangt in einen Luftverteilungsblock, der abwechselnd Luftdruck in die Luftkammern leitet und so die Membran zu einer hin- und hergehenden Bewegung zwingt, wodurch sich das Volumen der Arbeits- (Produkt-)kammer ändert und der Förderprozess erfolgt.
Diese Pumpen aus Kunststoffmaterialien – PP, PVDF – können recht aggressive Flüssigkeiten fördern, wie Schwefelsäure, Salpetersäure, Salzsäure, Säuregemische, galvanische Lösungen usw. Zudem ermöglicht die Konstruktion der Pumpe die Förderung von Flüssigkeiten mit einem gewissen Feststoffanteil, abhängig von der Pumpengröße.
Der Arbeitsdruck der Pumpe auf das Produkt wird typischerweise als eine Einheit geringer als der zugeführte Luftdruck angenommen. Der maximale Luftdruck beträgt 7 bar, entsprechend kann das Produkt mit etwa 6 bar gefördert werden. Technisch korrekt ist es jedoch, sich am Leistungsschaubild der Pumpe zu orientieren, das im Katalog für jedes Modell angegeben ist.
Im Diagramm sind die Luftdrücke mit roten Linien dargestellt, die Luftverbräuche mit schwarzen Kurven. An den Schnittpunkten dieser Linien kann man den Produktdruck und die Fördermenge bei gegebenem Lufteinlassdruck und Luftverbrauch ablesen.
Kein Wunder, dass solche Eigenschaften die Ingenieure und Verfahrenstechniker dazu bewegen, diese Pumpen in verschiedenen Filtrationsprozessen einzusetzen.
Beim Einsatz von Membranpumpen zur Filtration ist jedoch eine genaue Druckberechnung erforderlich, wobei das Funktionsprinzip der Pumpe berücksichtigt werden muss.
Erstens – die Membranpumpe fördert pulsierend, und ohne spezielle Dämpfer wird der Filter bei jeder Membranbewegung leichten Druckstößen ausgesetzt, was seine Lebensdauer erheblich verkürzen kann.
Zweitens – bei Verschmutzung des Filters steigt der Gegendruck in der Förderleitung, was zum vollständigen Stillstand der Pumpe führen kann.
Fazit – der Einsatz von Membranpumpen in Filtrationssystemen ist möglich und effektiv, sofern eine korrekte Auslegung und Auswahl der Ausrüstung erfolgt, insbesondere wenn andere Pumpentypen schwer oder gar nicht einsetzbar sind. In anderen Fällen sollten chemische Kreiselpumpen, Magnetkupplungspumpen oder Edelstahl-Kreiselpumpen bevorzugt werden.
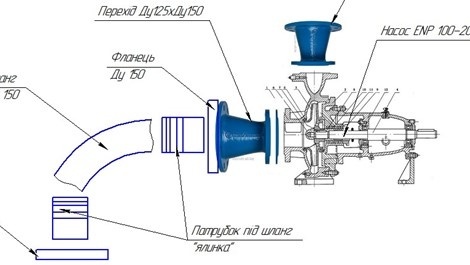
Die Hauptparameter nahezu jeder Pumpe sind ohne Zweifel die Fördermenge (in Kubikmetern pro Stunde, Litern pro Minute, Gallonen pro Minute usw.) und der von ihr erzeugte Druck (oder ein Vakuum, wenn es sich um eine Vakuumpumpe handelt).
Selbstverständlich stellt der Hersteller technische Daten zur Verfügung und garantiert, dass die Pumpe die angegebenen Werte leisten kann. Diese Angaben findet man in Katalogen, technischen Broschüren sowie auf dem Typenschild der jeweiligen Pumpe.
Neben den hydraulischen Parametern (maximale Fördermenge, maximaler Druck oder Nennwerte) sind auf dem Typenschild auch die Leistung des Elektromotors und seine technischen Daten angegeben.
Oft unbeachtet bleiben jedoch die Anschlussdurchmesser, also die Rohrdurchmesser für den Einlass und Auslass der Pumpe (im Englischen „Inlet“ und „Outlet“).
Auf den ersten Blick scheint es einfach – man nimmt Rohre mit den gleichen Durchmessern wie an der Pumpe angegeben. Doch diese scheinbar logische Annahme ist falsch und kann später zu vielen Problemen im Betrieb von Bewässerungs-, Zirkulations- oder Wasserversorgungssystemen führen.
Man muss verstehen, dass die Durchmesser der angeschlossenen Rohre durch eine hydraulische Berechnung bestimmt werden müssen. Das ist der einzig richtige Weg, Rohrdurchmesser auszuwählen. Wenn die Pumpe als Ersatz beschafft wird und ihre Werte nicht schlechter als die der alten sind, gibt es meist keine Probleme. Wird die Pumpe jedoch in einer neuen Anlage eingesetzt, ist eine hydraulische Berechnung zwingend erforderlich.
Man muss sich klarmachen: Eine Pumpe ist eine dynamisch arbeitende Maschine, und nur weil z. B. der Druckstutzen einen Nenn-Durchmesser DN50 hat, heißt das nicht, dass die Druckleitung ebenfalls DN50 haben muss.
Außerdem ist zu beachten, dass die vom Hersteller angegebenen technischen Daten unter bestimmten Prüfbedingungen ermittelt wurden. Bei freitragenden Kreiselpumpen gelten die Daten auf dem Typenschild für folgende Bedingungen:
Wassertemperatur 20°C;
Ansaughöhe 1,5 m;
Dichte der Flüssigkeit 1000 kg/m³.
In der Praxis weichen diese Werte meist ab. Besonders wichtig für Kreiselpumpen ist der Durchmesser der Saugseite. Damit die Pumpe nicht „erstickt“, keine Luft ansaugt und den gewünschten Druck liefert, muss der Durchmesser der Saugleitung stets größer sein als der Anschlussdurchmesser der Pumpe.
Ein Beispiel für das Verhältnis von Pumpen- und Saugrohrdurchmesser aus dem Katalog eines europäischen Herstellers:
Wie die Tabelle zeigt, muss der Durchmesser der Saugleitung größer sein, um einen ungehinderten Zulauf zur Arbeitskammer der Pumpe zu gewährleisten. Das ist besonders wichtig, wenn Wasser aus einer Tiefe von 4 Metern oder mehr entnommen wird. Bei zunehmender Ansaughöhe ändern sich die Förderkennlinien der Pumpe (Fördermenge und Druck nehmen ab).
Das folgende Bild zeigt ein typisches Beispiel für den Anschluss einer Pumpe zur Tröpfchenbewässerung, die Wasser aus einem Fluss unterhalb des Pumpenniveaus entnimmt.
Der Höhenunterschied zwischen Wasseroberfläche und Pumpenachse ist gering – nur etwa 1,5–2 m –, aber die Saugleitung ist etwa 5 m lang. Deshalb sollte eine Pumpe mit Saugstutzen DN125 mit einem größeren Rohr – mindestens DN150 – angeschlossen werden.
11 juli 2025
Durchflussregelung der Verdrängerpumpe
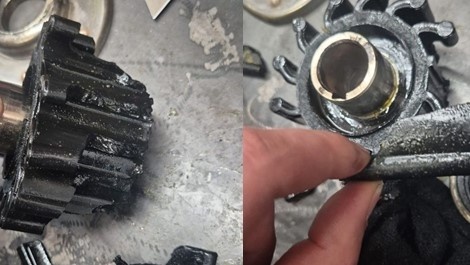
Verdrängerpumpen sind Geräte, die nach dem Prinzip der Volumenänderung der Arbeitskammer funktionieren. Dies kann durch einen exzentrisch montierten Impeller (in einer Impellerpumpe ), das Drehen von Zahnrädern , Kolbenbewegung, Membranbewegung , Änderung des Schlauchvolumens ( peristaltische Pumpe ) usw. erfolgen.
Aus dem Funktionsprinzip solcher Pumpen ergibt sich, dass ihre Leistung nicht durch das Schließen von Absperrventilen (auf der Druck- oder Saugseite) reguliert werden sollte – das kann schädlich und gefährlich für die Pumpe und das gesamte System sein.
Im Gegensatz zu dynamischen Pumpen erzeugen diese Pumpen keinen Druck, sondern überwinden vorhandenen Druck – dieser kann Dutzende oder sogar Hunderte von Megapascal (MPa) betragen.
Das bedeutet, dass z. B. eine Zahnradpumpe in einem Umlaufsystem tatsächlich den Widerstand des Rohrsystems (Rohre, Bögen, Filter) auf dem Manometer anzeigt.
Manometer in einem Transformator-Kühlsystem. Es arbeitet eine Zahnradpumpe ENP 1010 mit einem maximalen Druck von 15 bar. Das Manometer zeigt 0,2 bar an.
Darunter im Bild – das Ergebnis des Schließens des Ventils an der Druckleitung im selben System.
Durch das Schließen des Ventils wurde die Dichtungsgummierung beschädigt.
Ein weiteres Beispiel – der Versuch, den Durchfluss einer Impellerpumpe AlphaDynamic durch ein Ventil zu regeln.
Ergebnis – Impeller beschädigt und Reparatur notwendig.
Fazit – Die Leistung einer Verdrängerpumpe sollte mit einer Bypass-Leitung oder einem Frequenzumrichter geregelt werden. ES IST STRENGSTENS VERBOTEN, Absperrventile am Ein- oder Ausgang der Pumpe zu schließen. Falls kein Bypass installiert ist, müssen Sicherheitsventile vorhanden sein.
03 juli 2025
Besonderheiten des Betriebs von Nassläuferpumpen
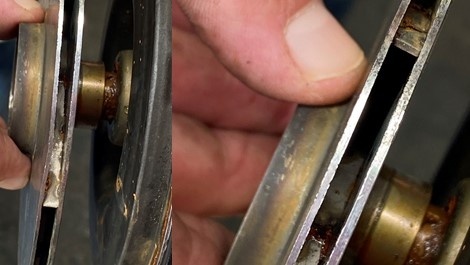
Pumpen mit „Nassläufer“ sind eine große Gruppe von Pumpen, die weit verbreitet in Heizungs- und Kühlsystemen eingesetzt werden.
Dank ihres geräuscharmen Betriebs, des geringen Energieverbrauchs und dem Fehlen einer Gleitringdichtung nehmen sie sowohl in industriellen als auch in privaten Heizsystemen eine bedeutende Nische ein.
Derzeit sind sowohl einfache Modelle – Einstufige Pumpen ohne Steuerung – als auch „intelligente“ Smart-Pumpen mit elektronischer Steuerung, Druck- und Durchflusskontrolle sowie verschiedenen Betriebsmodi erhältlich.
Trotz aller genannten Vorteile haben diese Pumpen einen wesentlichen Nachteil – die Qualität des Wassers oder Wärmeträgers, mit dem sie arbeiten. Unabhängig von der eingesetzten Elektronik bleibt das zentrale Element dieses Pumpentyps der mechanische Teil – der „Nassläufer“.
Da der Rotor vom Fördermedium umspült wird, muss dessen Qualität entsprechend hoch sein – sauber und frei von mechanischen Verunreinigungen (Zunder, Sand, Kalk usw.).
Auf dem Foto unten sehen Sie eine Pumpe, die nach nur 1,5 Monaten Betrieb wegen eines blockierten Rotors zur Wartung eingeschickt wurde.
Das Laufrad und der Spalt zwischen Rotor und Stator waren durch Zunder verstopft, was zum Blockieren des Rotors führte.
Fazit – bei der Verwendung solcher Pumpen ist eine sorgfältige Wasseraufbereitung unerlässlich. Bei guter Wasserqualität wird die Pumpe nicht nur die Garantiezeit überdauern, sondern auch viele Jahre zuverlässig arbeiten.
Andernfalls sollte man auf Pumpensysteme zurückgreifen, die weniger empfindlich gegenüber der Wasserqualität sind – Inline- Pumpen mit „Trockenläufer“ , die mit einem Standard-Asynchronmotor und einer Gleitringdichtung ausgestattet sind.
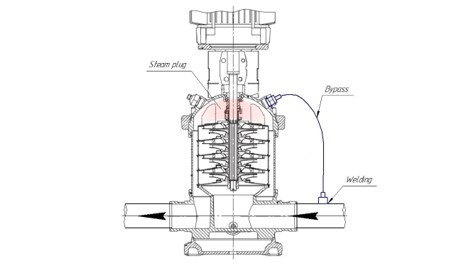
Kohlensäure oder Kohlenstoffdioxid (Kohlendioxid, Kohlenstoffoxid (IV), CO₂) – ein farbloses Gas (unter Normalbedingungen), das sich leicht in Wasser löst.
Abgesehen von der allgemein bekannten Tatsache, dass es ein wichtiger Bestandteil des Photosyntheseprozesses ist, wird diese Substanz in der Lebensmittel-, Pharma-, Landwirtschafts- und Maschinenbauindustrie weit verbreitet eingesetzt.
Im technologischen Prozess der Kohlendioxidproduktion ist der Einsatz von Transportmitteln für das Produkt unerlässlich, insbesondere einer Pumpeneinheit. Kohlendioxid befindet sich bei niedriger Temperatur und hohem Druck im flüssigen Zustand.
Auf dem Foto unten ist eine vertikale mehrstufige Pumpe zu sehen, die in einer Produktionslinie für Kohlensäure installiert ist. Auf der Oberfläche der Pumpe und der Absperrarmaturen ist Frostbildung (gefrorener Wasserdampf aus der Luft) zu erkennen.
Ein Merkmal dieses Pumpentyps ist die Fähigkeit, durch die Anzahl der auf einer Welle hintereinander angeordneten Laufräder einen hohen Druck zu erzeugen. Diese Konstruktion ermöglicht Druckwerte von 3 bis 25 bar.
Ein Nachteil der vertikalen Anordnung ist die Gefahr der Bildung von Dampf-Luft-Blasen im oberen Teil der Pumpe durch die hohe Strömungsgeschwindigkeit der Flüssigkeit, was zum lokalen Sieden von Kohlendioxid führen kann.
Gerade in diesem Teil der Pumpe befindet sich die Gleitringdichtung. Dieses Bauteil verhindert das Austreten von Flüssigkeit aus der Arbeitskammer und sollte durch die geförderte Flüssigkeit gekühlt werden. Da sich jedoch eine Dampf-Luft-Zone bildet, in der die Dichtung ohne Flüssigkeit arbeitet (sogenannter „Trockenlauf“), verringert sich die Lebensdauer der Dichtung erheblich.
Bei „Trockenlauf“ kommt es zu schnellem Verschleiß der Reibpaare und zum Schmelzen der Gummidichtungen.
Um dieses Problem zu lösen, kann ein Bypass-Rohr (Bypass) verwendet werden. Dieses Bauteil der Pumpenverrohrung ermöglicht die Ableitung der Dämpfe in die Saugleitung und verhindert so die Bildung einer Dampf-Luft-Blase im Bereich der Gleitringdichtung.
16 juni 2025
Manuelle Fasspumpen
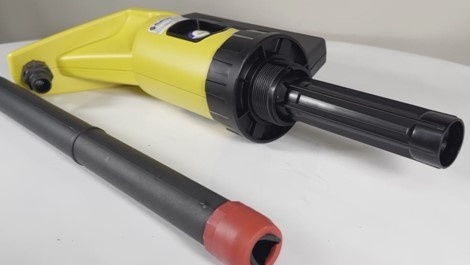
Manuelle Fasspumpen sind die optimale Lösung für kleine Unternehmen, Kfz-Werkstätten, Lebensmittelbetriebe – überall dort, wo Produkte abgefüllt oder kleine Mengen für einen bestimmten technologischen Prozess entnommen werden müssen.
Diese Pumpen können verwendet werden, um aus Großgebinden Motoröl, Pflanzenöl, Düngemittel, Enzympräparate, Pflanzenschutzmittel, Frostschutzmittel, Glykol, Alkohol, Dieselkraftstoff, Benzin usw. zu entnehmen.
Unsere Produktlinie manueller Fasspumpen wird vom italienischen Hersteller FLUIMAC angeboten.
Die „gelbe“ Pumpe, Modell N-04, ist für den Einsatz mit Kraft- und Schmierstoffen sowie fetthaltigen Produkten konzipiert.
Die Konstruktion der Pumpe ist einfach und zuverlässig. Die ausziehbare Saugstange ermöglicht den Einsatz in Behältern unterschiedlicher Tiefe, und die FKM-Gummidichtung gewährleistet chemische Beständigkeit und eine lange Lebensdauer.
Die „blaue“ Pumpe, Modell N-04 Blue, besitzt eine ähnliche Bauweise, jedoch mit einer PTE-Gummidichtung. Dadurch eignet sie sich für die Abfüllung von Säuren, Essig, Adipinsäure und anderen chemisch aggressiven Medien.
Die Fördermenge der Pumpe beträgt 0,3 Liter pro Hub, Anschlussgewinde ¾ Zoll.
Das teleskopische Saugrohr ist von 500 bis 950 mm verstellbar und hat einen Durchmesser von 34 mm.
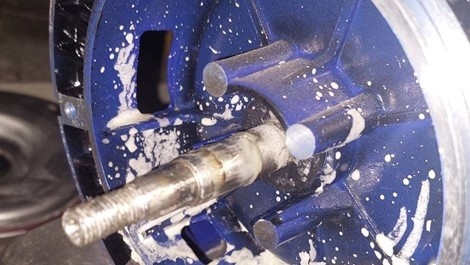
Für Produkte mit hoher Viskosität werden in der Regel Pumpentypen wie Impellerpumpen , Drehkolbenpumpen , Zahnradpumpen und Membranpumpen verwendet – also hauptsächlich Verdrängerpumpen.
Für bestimmte Produkte wie Öl, Transformatoröl, eine Mischung aus Wasser und Mehl im Verhältnis 1:4, Bierwürze, Maische und ähnliche Flüssigkeiten kann erfolgreich eine Kreiselpumpe mit offenem oder breitem Laufrad eingesetzt werden.
Ein wichtiger Punkt bei der Verwendung solcher Pumpen mit den oben genannten Medien ist die Notwendigkeit, die Pumpenkammer nach Abschluss des Fördervorgangs zu spülen.
Diese Art von Pumpenausrüstung ist mit einer Gleitringdichtung ausgestattet, die im Allgemeinen wartungsfrei ist. Wenn das Fördermedium jedoch zur Kristallisation, zum Anhaften oder zur Klumpenbildung neigt, kann dies zu Schäden an der Dichtung führen.
Auf dem folgenden Foto ist ein Schaden am Gummibalg der Gleitringdichtung zu sehen.
Dies geschah aufgrund einer nicht rechtzeitig durchgeführten Spülung der Pumpenkammer. Dadurch wurden die Reibflächen durch die stärkehaltige Mischung „verklebt“ und beim nächsten Start der Pumpe wurde der Gummibalg abgerissen.
In der Folge trat das Produkt aus der Arbeitskammer in den Raum zwischen Pumpenträger und Elektromotor aus.
In diesem Fall bemerkte der Bediener das Leck rechtzeitig und die Gleitringdichtung wurde ersetzt. Andernfalls hätte ein längerer Austritt des Mediums zu einem Schaden am Elektromotor führen können, was deutlich höhere Reparaturkosten und Verzögerungen im Produktionsprozess zur Folge gehabt hätte.
Unser Unternehmen bietet nicht nur den Verkauf von Pumpenanlagen und Ersatzteilen an, sondern auch fachkundige Beratung bei Auswahl und Wartung.
10 juni 2025
Vor- und Nachteile von Nassläuferpumpen
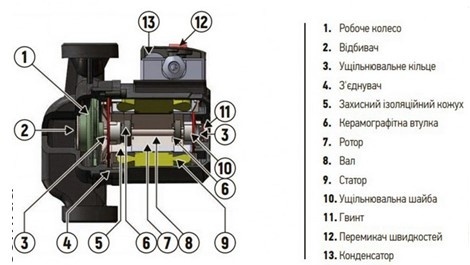
Pumpen mit „nassem Rotor“ verdanken ihren Namen einem Konstruktionsmerkmal – der Rotor der Pumpe wird von Gleitlagern gehalten und ist vollständig in Wasser eingetaucht.
Der Hauptvorteil dieser Konstruktion ist der geräuscharme Betrieb. Da der Rotor auf Gleitlagern rotiert und keinen Lüfter zur Kühlung besitzt, arbeitet die Pumpe äußerst leise. Manchmal lässt sich die Drehung des Rotors nur mit einem Magnetindikator feststellen.
Ein weiterer Vorteil dieser Bauweise ist das Fehlen von Dichtungen. Es handelt sich um eine nahezu hermetisch geschlossene Pumpe, die nur eine Entlüftungsschraube besitzt.
Darüber hinaus sind die meisten Pumpen mit „nassem Rotor“ mit einem Drehzahlregler ausgestattet, der es ermöglicht, die Pumpe auch bei kleinen Berechnungsfehlern optimal an das Heizsystem anzupassen.
In privaten Heizsystemen sowie in Heizzentralen von Mehrfamilienhäusern, bei denen ein niedriger Geräuschpegel entscheidend ist, sind diese Pumpen nahezu alternativlos.
In industriellen Heizsystemen, Heizkesseln, Holztrocknungsanlagen oder in Kühlkreisläufen der Lebensmittelindustrie zeigt diese Bauweise jedoch ihre Schwächen.
Da der Spalt zwischen Rotor und Stator sehr gering ist (0,5–2 mm, je nach Modell), sind die Anforderungen an die Wasserreinheit sehr hoch. Das Eindringen von Rost, Schmutz, Dichtungsresten oder Schweißelektroden nach Reparaturen kann zum Ausfall der Pumpe führen.
Dieser Pumpentyp ist nur schwer zu reparieren. In der Regel führen Servicefirmen keine Einzelreparaturen am Rotor oder Stator durch und tauschen auch keine Keramiklager separat aus. Stattdessen wird die gesamte Pumpeneinheit ersetzt, was etwa 80 % des Gesamtpreises der Pumpe ausmacht.
Ein weiterer wesentlicher Nachteil – insbesondere bei industriellen Anwendungen – ist der Preis. Viele führende Hersteller wie Wilo, Grundfos oder DAB haben mechanisch schaltbare Modelle eingestellt und bieten nun vergleichbare Modelle mit Frequenzregelung an, die teilweise mehr als doppelt so teuer sind wie die alten Varianten.
Eine mögliche Alternative für den Austausch nicht mehr produzierter europäischer Pumpen könnten einzelstufige Pumpen mit „nassem Rotor“ von EDWIN oder Inline-Pumpen mit „trockenem Rotor“ mit einem herkömmlichen Asynchronmotor sein.
06 juni 2025
Kauf von Sonnenkollektoren
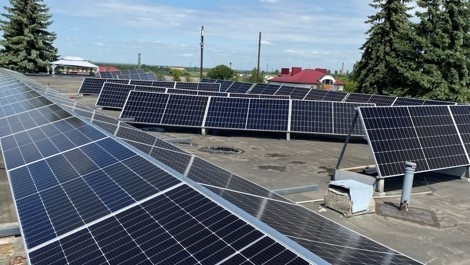
Die ersten Prototypen von Solarmodulen wurden bereits Mitte des 19. Jahrhunderts erfunden. Sie wurden anschließend weiterentwickelt und immer beliebter, doch erst in den letzten acht Jahren haben sie sich massiv verbreitet. Heute ist Solarenergie nicht nur eine wirtschaftlich sinnvolle Investition, sondern auch eine umweltfreundliche Lösung für ökologische Probleme. Solarmodule reduzieren CO2-Emissionen und helfen so, die globale Erwärmung und den Klimawandel zu bekämpfen.
Vor dem Kauf von Solarmodulen sollte man entscheiden, ob sie für den Eigenverbrauch oder zum Verkauf bestimmt sind. Wenn eine Privatperson mit dem System Einkommen erzielen möchte, darf die Leistung 30 kW nicht überschreiten. Bei Eigenverbrauch wird die Anlage an den Verbrauch angepasst.
Die Module unterscheiden sich in Leistung und Material: monokristallin (am häufigsten) und amorph.
Angenommen, du brauchst 10 kW Leistung und wählst Module mit 560 W.
Gesamtleistung durch die Leistung eines Moduls teilen.
15–20 % Reserve hinzurechnen, um Verluste auszugleichen.
10 000 W / 560 W = 17,8 Module
Mit 15–20 % Zuschlag: 17,8 * 1,15 = 20,47 → aufrunden auf 21 Module.
Um eine 10 kW-Anlage zu betreiben, werden also 21 Solarmodule benötigt.
Solche Module kannst du direkt bei uns kaufen, einfach hier klicken .
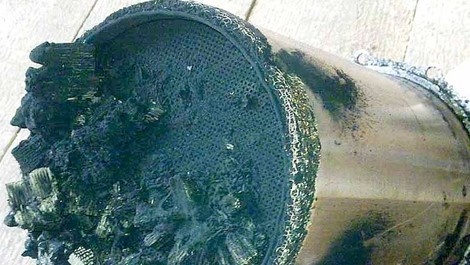
Partikelfilter sind eines der Hauptbestandteile des Abgassystems eines Fahrzeugs. Dieses Gerät sorgt für die Reinigung der Abgase von Verbrennungsmotoren von festen Staubpartikeln, die bei der Verbrennung von Kraftstoff entstehen – Ruß.
Moderne Fahrzeugmotoren sind mit automatischen Systemen zur Regeneration des Filters ausgestattet, die ohne Eingreifen des Fahrers arbeiten. Mit der Zeit jedoch wird diese Reinigung unzureichend, und der Filter muss zur Reinigung in Spezialanlagen ausgebaut werden.
Es gibt zwei Hauptmethoden zur Reinigung des Partikelfilters – chemisch und hydrodynamisch . Die chemische Methode erfordert den Einsatz spezieller Reagenzien und entsprechender Ausrüstung.
Im Gegensatz dazu ist die hydrodynamische Methode kostengünstiger und umweltfreundlicher. Sie ermöglicht die Wiederherstellung von bis zu 98 % der Filterkapazität.
Das Hauptelement der hydrodynamischen Reinigungsanlage ist eine Kreiselpumpe . Je nach Filtertyp werden Pumpen mit Durchflussraten von 50 bis 150 l/min und einem Druck von 4–7 bar verwendet.
Die Reinigungsanlage kann vom Zirkulations- oder Durchfluss-Typ sein. In Zirkulationsanlagen (wo verschmutztes Wasser gefiltert und wiederverwendet wird) empfiehlt sich der Einsatz von Ein- oder Zweistufenpumpen mit einem Druck von 4–5 bar.
Diese Pumpen haben ein Laufrad, das breit genug ist, um ein Verstopfen durch Ruß- und Schmutzpartikel zu verhindern.
In Durchflusssystemen können vertikale mehrstufige Hochdruckpumpen (5–7 bar) verwendet werden. Das Spülwasser gelangt nicht zurück in die Pumpe, sondern wird in die Kanalisation abgeleitet, wodurch das Risiko einer Verschmutzung der Durchflusskomponenten ausgeschlossen ist.
Unsere Spezialisten stehen Ihnen jederzeit zur Verfügung, um Sie bei der Auswahl von Pumpenausrüstung für Partikelfilter-Reinigungsanlagen zu unterstützen.