2024 — Prom-nasos.com.ua
December 13, 2024
Pumps for swimming pools
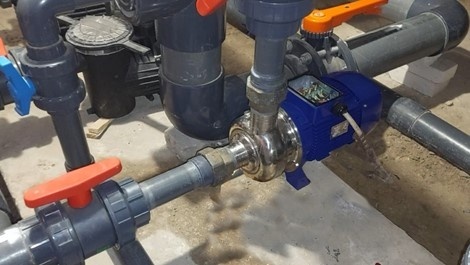
Swimming pool pumps are conventional centrifugal pumps. The only difference is that they usually have an integrated coarse filter (see Fig. 1), the so-called ‘hair filter’, in their housing.
In general, the prefix ‘pumps for water supply, heating, well or swimming pool’ is determined by the system or place where the pump will be used. Accordingly, the same pump can be used in different systems. That is, no one prohibits the use of a water supply pump in a pool circulation system, as long as it meets the required parameters.
Pumps used in swimming pool filtration and circulation systems must provide sufficient water supply, which depends on the volume of the pool. The pressure created by the pump is usually in the range of 1 to 2 atm. This pressure is quite sufficient both for circulation and to overcome the resistance of the filtering system (sand filters).
Since the water in the pool is disinfected, it contains a small concentration of sodium hypochlorite, so the material of the flow part should be made of plastic or stainless steel.
The absence of an integrated filter can be easily compensated for by using a conventional coarse filter in the suction line. When using pumps with an open impeller (see Fig. 2), a filter can be dispensed with, as this type of impeller does not clog, and impurities and dirt are further stopped by the sand filter and do not re-enter the pool.
Our specialists have successfully replaced a classic plastic pool pump with a centrifugal stainless steel pump.
Since the pump to be replaced had failed due to a motor winding burnout, a protection and control panel was also installed to control the new pump and the protection parameters were adjusted accordingly.
Pump that has failed
New pump
December 5, 2024
Problems when starting a self-priming pump and solutions
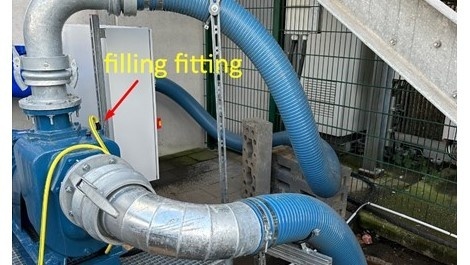
Self-priming pumps with a pre-filling chamber can operate without installing a check valve at the end of the pipe. These pumping units are convenient for unloading tanks with oil products, diesel fuel, petrol, oil and other liquids.
The ability to suck in liquid is ensured by the built-in check valve and the design of the pump casing, which stores a certain level of liquid to start the pump. However, for the first start, there still needs to be liquid in the working chamber, so you will have to fill it up the first time. For this purpose, a filler connection is provided on the casing (see Fig. 1 item 4, Fig. 2).
The table below shows typical faults that may occur during operation of a centrifugal self-priming pump and how to resolve them.
November 29, 2024
Energy-saving pumps with frequency converter
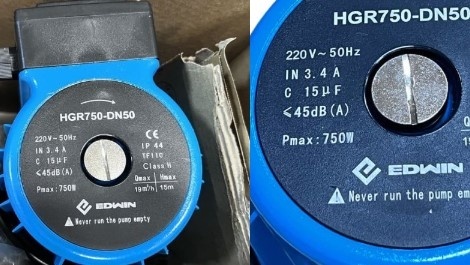
Pumps are indispensable devices in many industries, from heating systems to industrial equipment. Choosing the right pump can significantly improve system efficiency and reduce energy costs. Let's take a look at the features and benefits of these pumps.
Energy-saving pumps are used to optimise energy consumption. They are designed to reduce energy consumption while performing their functions. This is achieved through the use of innovative technologies, such as integrated control systems that adapt the pump to changing conditions. For example, circulation pumps with a frequency converter allow you to adjust the rotor speed, which makes it possible to operate only within the required capacity. This is an ideal solution for heating and water supply systems.
The use of a frequency converter reduces energy consumption, ensures a steady flow and avoids overloading the system. The variable pump speed allows the pump to be precisely adjusted to the needs of the system, which is important for energy conservation.
You can find out more about the circulation pump with frequency converter here.
November 25, 2024
Types of wind turbines
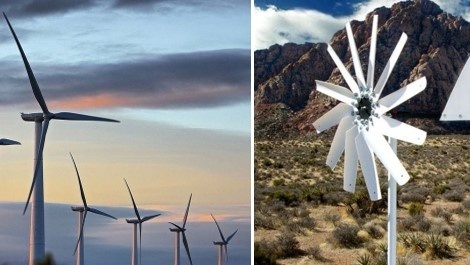
Tulip and H-type wind turbines have different designs and operating principles:
Tulip wind turbines
Design: Vertical wind turbines with a cylindrical shape and curved blades resembling tulip petals.
Advantages:
Effectively operate at low wind speeds, making them ideal for urban and suburban areas.
Reduce noise and vibration due to their shape.
Require less space for installation.
Less hazardous to birds and bats.
Easier to maintain and repair.
H-type wind turbines
Design: Horizontal wind turbines with blades arranged on a horizontal axis.
Advantages:
High efficiency at high wind speeds.
Often used for large wind farms due to their power.
Can generate more energy in stable wind conditions.
Both types have their advantages and disadvantages, and the choice depends on specific conditions and needs.
In addition to the tulip and H-type wind turbines, there are several other main types of wind turbines:
Horizontal wind turbines (HAWT)
Design: The blades are arranged on a horizontal axis.
Advantages:
High efficiency in stable wind conditions.
Often used in large wind farms, both on land and at sea.
Vertical Wind Turbines (VAWT)
Design: Blades are arranged on a vertical axis.
Advantages:
Can operate in variable wind directions.
Easier to maintain as generator and transmission are located closer to the ground.
Other types of wind turbines
Savonius: Vertical wind turbines with two or more curved blades that resemble a drum shape. Used for small installations.
Darrieus: Vertical wind turbines with “C” or “H” shaped blades. They are effective at high wind speeds.
Bladeless wind turbines: Use vibrations to generate power, which reduces noise and vibration.
Each type has its own unique characteristics and is suitable for different conditions and needs.
For a detailed overview of the principle of operation and the choice of the desired model, you can go to the website.
November 22, 2024
Iron-phosphate batteries LiFePO4/LFP
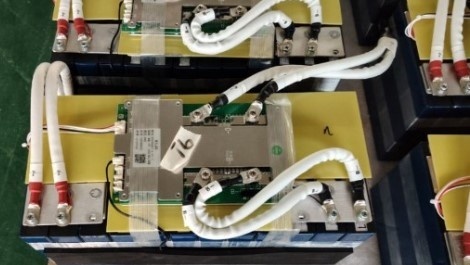
Iron-phosphate batteries, also known as lithium-iron-phosphate batteries (LiFePO4 or LFP) , are a type of lithium-ion battery that has gained popularity due to their safety, durability and stable performance. These batteries differ from other lithium-ion batteries, such as lithium-cobalt-oxide (LiCoO2) batteries, due to their chemical structure, which gives them certain advantages and disadvantages.
Main characteristics of LFP batteries
Chemical composition: Iron phosphate (LiFePO4) is used as the cathode material, while the anode is traditionally made of graphite. The iron phosphate structure provides high resistance to thermal changes, which increases the overall safety of the battery.
Safety: Due to their stable chemical structure, LFP batteries are less prone to overheating and are not prone to thermal runaway, which makes them less vulnerable to fire. This is a significant advantage over other lithium-ion batteries, which can be prone to spontaneous combustion.
Long service life: One of the main advantages is a long cycle life - LFP batteries can withstand 2000-4000 charge-discharge cycles, while retaining most of their capacity. Some high-end models can even exceed 5,000 cycles.
High discharge tolerance: These batteries can be discharged to lower voltage levels without significantly affecting their lifespan. This makes them suitable for applications that require regular deep discharges.
Environmentally friendly: Unlike batteries containing cobalt or nickel, the production of LFP batteries has a lower environmental impact, as iron and phosphate are less toxic and easier to recycle.
Areas of application
LFP batteries are used in a variety of applications, including:
Electric Vehicles: Due to their safety and long cycle life, many electric vehicles use LFP batteries, especially models aimed at the mass market.
Energy Storage Systems: Due to their deep discharge resistance and long life, they are ideal for home and commercial energy storage systems.
Portable Devices and Equipment: They are used in a variety of portable devices and electrical equipment where safety and durability are critical factors.
To learn more about how it works and how to choose the right model, visit the website.
September 20, 2024
Buying a generator
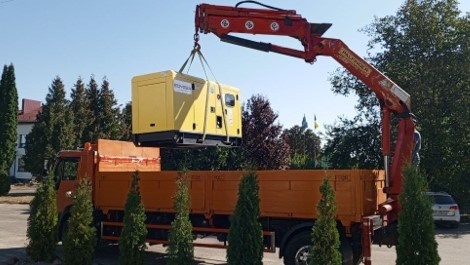
The modern world requires a reliable power supply, especially for businesses and private households. Installing a generator is a smart solution to ensure uninterrupted operation of equipment, lighting and other critical needs.
The photo shows the delivery of a new generator using a truck crane. This is an important part of the process, as it ensures the safe movement of heavy equipment, which, in this case, has a yellow casing and markings SOYGEN .
Advantages of installing a generator:
Autonomy: Provides uninterrupted power supply during power outages.
Reliability: High quality generators, such as the one shown in the photo, can operate in a variety of conditions, providing stable power.
Savings: The use of a generator can reduce electricity costs in conditions of unstable supply or in case of accidents.
Before to buy a generator , you should determine its purpose and required power, as well as pay attention to the technical characteristics and quality of the equipment. The installation should be entrusted to specialists who will be able to choose the right place and make all the necessary settings.
By choosing a generator, you invest in your own comfort and safety!
August 30, 2024
Installation of a wind turbine
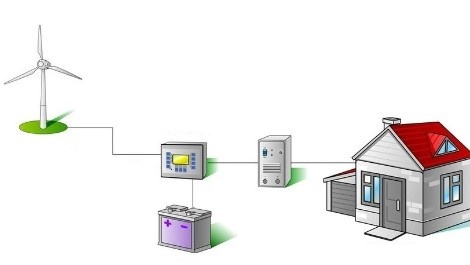
Choosing a wind turbine
The choice of wind turbine depends on your electricity needs. There are different types of wind turbines:
Vertical wind turbines : Suitable for private homes and capable of producing from several hundred watts to several kilowatts of electricity.
Horizontal wind turbines : Used for small commercial enterprises and can produce from a few kilowatts to several tens of kilowatts.
Preparation of Tools and Equipment
To install a wind turbine, you will need the following tools and materials:
Foundation bolts;
Crane or hoist ;
Electrical cables ;
Inverter (for converting alternating current to direct current);
Protective equipment (helmets, gloves, etc.).
Installation of the Foundation
The foundation is an important part of the wind turbine construction. It must be strong enough to support the weight of the generator and withstand strong winds.
Dig a foundation hole according to the dimensions and requirements of your wind turbine.
Install the rebar and pour concrete to create a strong foundation.
Fix the foundation bolts in the concrete until it hardens.
Installation of the Pillar
Once the foundation has hardened, the installation of the pole can begin.
Use a crane or hoist to lift the pole and place it on the foundation.
Fix the post with foundation bolts and check its verticality.
Installation of a wind turbine
The next step is to install the wind turbine itself on the pole.
Lift the wind generator with the crane and attach it to the top of the pole.
Connect the electrical cables from the generator to the inverter and the energy storage system (battery).
Connect and configure
After the generator is physically installed, it must be connected to the electrical system.
Connect the inverter to the generator and to your power grid.
Adjust the charge controller for optimal operation of batteries .
Check all connections and make sure they are secure.
Testing and Launch
After the installation is complete, test the system:
Check the operation of the wind generator at different wind speeds.
Ensure that electricity is generated and delivered to your grid or storage system.
Adjust settings for optimal performance.
Conclusion
Installing a wind turbine is a complex but important process that will allow you to harness renewable energy to power your home or business. If you follow all the steps correctly, you will be able to ensure stable and reliable operation of your system. If you encounter any difficulties, it is recommended that you contact a professional to install and configure your wind turbine.
August 29, 2024
Types of wind turbines
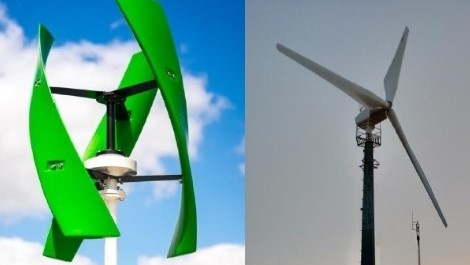
Wind turbines are an efficient way of harnessing wind energy to generate electricity. They can be used in both private households and commercial enterprises. Wind turbines are an increasingly popular source of renewable energy that harness the power of the wind to generate electricity, reducing dependence on traditional fossil fuels. There are two main types of wind turbines: horizontal and vertical .
Horizontal wind turbines (HAWT)
Horizontal wind turbines are the most common and most efficient. Their blades are perpendicular to the ground and the main shaft is parallel. They resemble classic windmills with long, thin blades. These generators work best at high wind speeds and are often used in large wind farms.
Advantages:
High efficiency under optimal conditions.
Well-developed technologies for large-scale production.
Highest power among available options.
Disadvantages:
High initial cost.
The need for a complex management system.
Vulnerability to strong winds and turbulence.
Vertical wind turbines (VAWT)
Vertical wind turbines have an axis of rotation that is perpendicular to the ground. Their blades are arranged around a shaft, allowing them to operate regardless of wind direction. This makes them ideal for urban environments and locations with variable winds.
Advantages:
Simplicity in installation and maintenance.
Efficient operation at low wind speeds.
Less impact on the environment and aesthetic appearance.
Disadvantages:
Lower efficiency compared to horizontal wind turbines.
Limited power making them less suitable for large projects.
Conclusion
The choice between horizontal and vertical wind turbines depends on the specifics of the terrain, climatic conditions and power requirements. For large wind farms with high wind speeds, horizontal wind turbines are the best option. At the same time, vertical wind turbines are ideal for urban environments and locations with variable wind conditions, where their versatility and simplicity are key advantages.
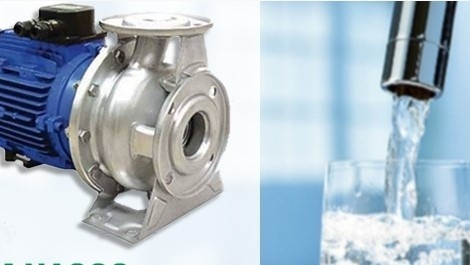
Pumping equipment with a high capacity, and therefore a large volume of water that can be moved per unit of time, makes up a much smaller percentage of the total number of pumps used in industry and agriculture.
These pumps are used by local water utilities, heat supply companies to supply drinking water or heat supply of villages, towns or even entire neighborhoods of large cities. In addition, these pumps can be used for water lowering , water storage for irrigation and irrigation in agriculture , pumping water from construction pits, etc.
As a rule, when the question arises of quick delivery of a pump whose power is greater 20-30 kW , to start production or solve an emergency situation, the supply department faces the problem of long delivery times and prices.
Our company is ready to offer high-capacity pumps in stock in Ukraine at the best prices.
In particular, these are compact (despite high power) pumps of the design in-line .
For example, there are such models available as IRG 200-315(I) , IRG 100-200 (I) , IRG 200-315 (I) A.
These pumps are very convenient to install, as the motor is placed vertically, and the pressure and suction nozzles are on the same line. The vertical placement of the motor also prevents the electric motor from flooding if the end seal is damaged.

Self-priming and normally aspirated pumps
Theory
The maximum theoretical depth from which any pump on planet Earth can raise a liquid is minus one physical atmosphere, in meters of the water column, it is approximately 10.3 m. That is, there is no pump that can draw a liquid from a greater depth (no centrifugal , not vacuum , or diaphragm or any other).
Another misconception is that a pump with a power of, for example, 11 kW can ‘pull’ liquid from a greater depth than a pump with a power of 0.55 kW. The power of the pump affects its capacity and pressure, and has no bearing on the depth from which it can draw fluid.
Practice
Normal suction pumps
In fact, the vast majority of pumping units are normally suction pumps. This includes the entire group of centrifugal pumps, which are dynamic pumps (with a spiral impeller, vortex, radial or other). These pumps cannot self-priming (pull liquid without being primed) because when they start up, without liquid in the working chamber, they are essentially pumping air, and since the density of air is much lower than that of any liquid, the suction force (vacuum) is not sufficient.
In order to start such a pump unit, it is necessary to first fill the working chamber of the pump with liquid (water, alcohol , ethylene glycol, milk etc.). In addition, if the liquid level is below the axis of the suction pipe, a non-return valve must be installed at the end of the pipe, so that after stopping the pump, the liquid remains in the working cavity and it is possible to start working again.
A group of pumps with a pre-priming chamber should be selected separately. Although they are conventionally called self-priming, in fact these pumps are also normally priming and also require the presence of liquid in the working chamber to start work. The only difference is that you only need to fill the pump once, since the presence of a pre-filling chamber allows you to keep a reserve of liquid sufficient to start the pump. Accordingly, this feature allows the use of such pumps without a non-return valve.
Self-priming pumps
In most cases, when people talk about a ‘self-priming’ pump, they mean a unit that can draw liquid without pre-filling, simply by throwing a hose or lowering a pipe into the liquid.
Displacement pumps have this property - piston, diaphragm , impeller , peristaltic , roller pumps etc. The principle of operation of these pumps is based on a change in the volume of the working chamber, as a result of which they can draw liquid without filling.
This feature is very useful when working with aggressive substances, such as acids, alkalis, mineral fertilisers and other liquids, when it is not possible to fill the working chamber.
This group includes the vast majority of pipette pumps (plunger, diaphragm, peristaltic). Simply lower the suction nozzle (hose) into the reagent and switch on the pump, and the process of filling the working chamber and further operation will begin automatically.