May 2024 — Prom-nasos.com.ua
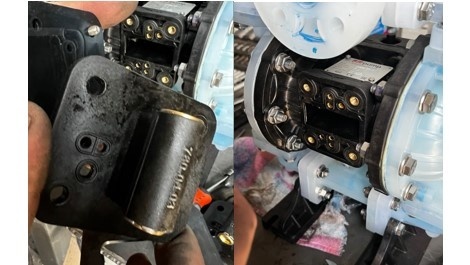
BASIC RULES
Effective and trouble-free operation of a diaphragm pump , like any other type of equipment, must begin with installation in accordance with all the rules. This will make your life much easier. A solid foundation, correct pipeline geometry, sufficient diameter of pipes - at least one aspect was missed, and now vibrations, increased pressure and other negative factors begin their destructive activities. Maintenance of the diaphragm pump does not tolerate neglect of the instructions. It is necessary to tighten the housing nuts before commissioning - do this. Testing is provided with measuring the flow and pressure of the unit at certain parameters of air flow and pressure - carry it out.
A common cause of breakdown of a diaphragm pump or a decrease in its productivity lies in the incorrect use of the pneumatic pump, or neglect of the operational requirements stated in the pump passport. The pneumatic diaphragm pump is simple in design and works with thick and viscous liquids, including glue, acids or food. Can pump abrasive particles with a diameter of up to 10 mm. But if used incorrectly, advantages can turn into disadvantages.
Before starting to operate a diaphragm pump, it is of great importance to select the correct elements of air preparation, filters, moisture separators, pressure reducing valves, etc. Pressure filters include air filters (inlet, fine, inline, high pressure or stainless steel) and water filters. Air filtration using inlet filters removes coarse contaminants. Air filtration is at the level of 20 um, in the case of large filters - 50 um. Inlet filters are installed immediately after the compressor. It is worth remembering that frequent replacement of filter cartridges improves the quality of the compressed air at the outlet. In the case of thin filters, installation should be carried out at the compressed air intake points. Their task is to prepare the air under the specified conditions. Fine filters should always precede the inlet filter. Depending on the application, air filtration is 5 microns, 0.3 microns or even 0.01 microns. On the other hand, in-line filters are installed where there is no physical space for standard filters. They are very often used in front of pneumatic tools. The air filtration of such filters is 20-30 microns. Improper preparation of the air supplying the pump can lead to failure of the pump, or its main parts, such as rubber products and, in general, the pneumatic valve of the diaphragm pump.
Installation of an air operated diaphragm pump
Before the pump, air preparation ( reducer, filter-moisture separator, throttle ).
Pneumatic line of sufficient diameter.
Only horizontal placement of the pump.
Since diaphragm pumps are self-priming, it is important for them to ensure tight connections .
Before turning on, be sure to check that there are no foreign objects in the pump , that the seals have been broken and that the screws are tightly tightened .
The diaphragm pump can be installed both on the floor and on the ceiling, it is important that the pump is installed horizontally (standing on its feet), the fluid supply manifold is at the top of the pump (pay attention to the arrows that are drawn on the pump, they indicate the correct direction, the arrow should point upward as shown in the figure).
! VERY IMPORTANT ! Such an industrial pump should be located as close as possible to the place where the liquid is pumped and from where it is taken. This will ensure maximum performance. As you know, the longer the hoses and the more viscous the liquid, the greater the deviations in pump performance from those stated in the passport.
Starting the diaphragm pump
The valve balls must be moistened with hydraulic fluid before starting the pump. The pump must be dried from water if water is not allowed to enter the pumped liquid. Initially, there may be water in the diaphragm pump, since its functionality is checked by pumping water before shipping.
Basic rules for servicing a diaphragm pump
Many aspects of using a diaphragm pump are intuitive. But we want to focus on the key ones.
A superficial inspection of the pump should be done at least once a month to replace filters as necessary and check the integrity of the pump. If there is liquid under the pneumatic cap, this is a bad sign; most likely a crack has formed somewhere and this may soon lead to the final breakdown of the pump. In this case, you can immediately contact us to replace damaged parts, inspect, or, in extreme cases, purchase a similar pump.
Replacement of parts is carried out in a clean and dry room. Parts are replaced only with new, original ones.
Before disassembling the diaphragm pump (depending on the pumped liquid), the technician must wear gloves and goggles , in case of working with toxic substances.
Before disassembling the pump, you need to WASH it to get rid of toxic liquids as much as possible.
Before disassembling after washing the pump, it is necessary to DISCONNECT from the compressor, DISCONNECT the inlet and outlet pipes.
Then you can proceed directly to disassembling the diaphragm pump, if necessary.
! VERY IMPORTANT ! If the pump is rarely used, or you plan to postpone the operation of the equipment for some time, It is NECESSARY to flush the pump of the pumped substance to avoid sticking of the channels.
AIR CONNECTION DUCT HUMIDITY
The presence of water in the compressed air system can cause problems such as freezing of the water or icing of the discharge line, causing the pump to run unevenly or stop. These problems can be overcome by using a point-of-use dehumidifier in addition to the user's air drying equipment. Air drying equipment will remove water and eliminate problems such as freezing or icing.
The air pressure should not exceed 7 bar. The pump must be supplied with air at a pressure and flow rate to provide the desired performance.
AIR VALVE LUBRICATION
The pump should be flushed after each use to prevent damage if the pump is used to pump liquids containing suspended particles that will settle and harden over time while the pump is stationary. (Otherwise, product left in the pump between uses may dry out or settle. This may cause problems with the diaphragms and check valves when restarted.) The pump should be completely drained after each use, especially in freezing temperatures.
1 post