2025 — Prom-nasos.com.ua
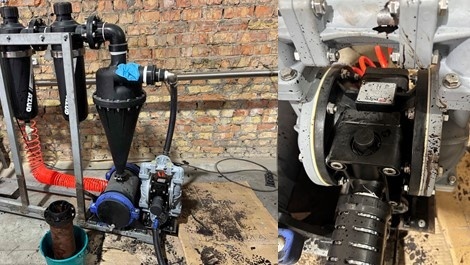
DP series diaphragm pumps from the Turkish manufacturer Diapump are pumps driven by compressed air. The compressed air enters the air distribution block, which alternately directs pressure into the air chambers, causing the diaphragm to perform reciprocating movements, changing the volume of the working (product) chamber and enabling the pumping process.
These pumps, made of plastic materials – PP, PVDF – can handle quite aggressive liquids such as sulfuric, nitric, hydrochloric acids, acid mixtures, galvanic solutions, etc. Additionally, the pump design allows for pumping liquids with a certain content of solid particles depending on the pump model.
The working product pressure of the pump is considered to be one unit lower than the air pressure supplied. The maximum air pressure is 7 bar, so the product can be pumped at about 6 bar. However, the technically correct approach is to refer to the pump’s performance chart provided in the catalog for each model.
On the chart, the red lines represent air pressure, while the black curves represent air consumption. At the intersection of these lines, one can determine the resulting product pressure and flow rate depending on the inlet air pressure and consumption.
It’s no surprise that these pump features encourage engineers and technologists to use them for filtration in various technological processes.
However, when using a diaphragm pump for filtration, one must carefully calculate the pressure and take into account the pump’s operating principle.
First – the diaphragm pump produces a pulsating flow, and without special dampers , the filter will be exposed to minor hydraulic shocks with each diaphragm movement, which can significantly shorten the filter’s service life.
Second – as the filter becomes clogged, the backpressure in the product supply line increases, which may lead to the complete stop of the pump.
Conclusion – the use of diaphragm pumps in filtration systems is possible and effective, provided proper selection and calculation of the equipment, and when other pump types are difficult or impossible to use. Otherwise, preference should be given to centrifugal chemical pumps, magnetic drive pumps , or stainless steel centrifugal pumps.
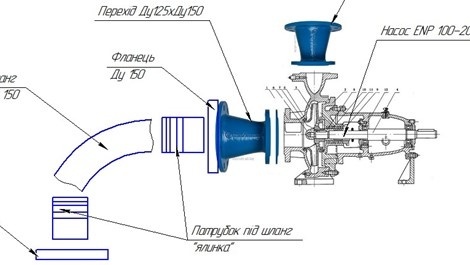
The main parameters of almost any pump are undoubtedly the flow rate (in cubic meters per hour, liters per minute, gallons per minute, etc.) and the pressure it generates (or vacuum, if it's a vacuum pump).
Of course, the manufacturer provides the pump’s technical specifications and guarantees that the pump can deliver the stated performance. These parameters are listed in catalogs, technical brochures, and also marked on the nameplate of the specific pump.
In addition to hydraulic data (maximum flow rate, maximum pressure or nominal values), the nameplate also includes the electric motor power and its characteristics.
However, the connection diameters, i.e., the inlet and outlet sizes to which the pump is connected in the system (marked “Inlet” and “Outlet” in English), are often overlooked.
At first glance, it seems simple – connect pipes that match the pump’s inlet and outlet diameters. But this seemingly logical assumption is actually incorrect and may lead to various issues during the operation of irrigation, circulation, or water supply systems.
It is essential to understand that the diameters of pipes connected to the pump must be determined through hydraulic calculation. This is the only correct way to select pipeline diameters. When replacing an old pump, if the new one has equal or better parameters, it usually works fine. But for a pump in a new system, hydraulic calculations must be done.
One must also remember that a pump is a dynamic machine, and the fact that the discharge port is, for example, DN50 does not mean the discharge pipe must be DN50 as well.
It’s also important to note that the parameters provided by the manufacturer in the documentation are based on specific test conditions. For example, for centrifugal overhung pumps, the nameplate data are based on the following:
water temperature of 20˚C;
suction depth of 1.5 m;
liquid density of 1000 kg/m³.
In real-world conditions, these parameters often differ. Suction pipe diameter is especially important for centrifugal pumps. To avoid air suction, cavitation, and performance loss, the suction pipe must always be larger than the pump’s suction port.
An example of pump and suction pipe diameter ratios as given in the catalog of a European manufacturer:
As shown in the table, the suction line diameter should be larger to ensure proper fluid flow into the pump’s working chamber. This is especially important when water is drawn from a depth of 4 meters or more. As suction depth increases, the pump’s flow-pressure characteristics change (i.e., reduced flow and pressure).
The image below shows a typical setup of a drip irrigation pump that draws water from a river, below the pump installation level.
The height difference between the water surface and the pump axis is small – only 1.5–2 m – but the suction pipe length is about 5 m. Therefore, a pump with a DN125 suction port should be connected with a larger pipe – at least DN150.
July 11, 2025
Flow control of a positive displacement pump
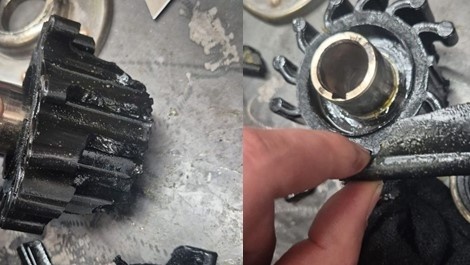
Positive displacement pumps are devices that operate based on the principle of changing the volume of a working chamber. This can occur due to an eccentrically mounted impeller (in an impeller pump ), rotation of gears , piston movement, membrane movement , change in hose volume ( peristaltic pump ), etc.
Given the operating principle of such a pump, it can be concluded that regulating its performance with shut-off valves (by closing valves on the discharge or suction line) may be harmful and dangerous both to the pump and the system in which it operates.
Unlike dynamic pumps, these pumps do not generate pressure but are capable of overcoming certain pressure, which may reach dozens or even hundreds of megapascals (MPa).
This means that if, for example, a gear pump is operating in a circulation system, the pressure gauge will actually show the resistance of the piping system (pipes, bends, filters).
Pressure gauge in a transformer cooling system. A gear pump ENP 1010 is operating with a maximum pressure of 15 bar. The pressure gauge shows 0.2 bar.
Below in the photo – the result of closing the valve on the discharge pipe in the same system.
As a result of closing the valve, the sealing rubber was damaged.
Another example – an attempt to regulate flow with a valve in an impeller pump AlphaDynamic .
As a result – damage to the impeller and the need for repair.
Conclusion – the operation of a positive displacement pump should be regulated using a bypass line or frequency inverter. IT IS STRICTLY FORBIDDEN to close shut-off valves at the pump inlet or outlet. If a bypass line is not installed in the system, safety valves must be used.
July 3, 2025
Peculiarities of wet rotor pumps operation
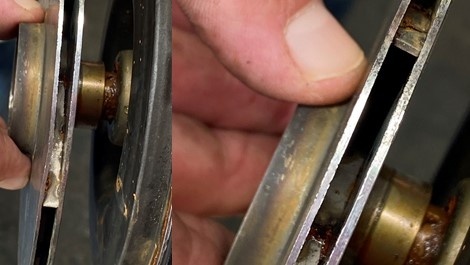
Wet rotor pumps are a large group of pumps widely used in heating and cooling systems.
Thanks to their silent operation, low energy consumption, and absence of mechanical seals, they occupy a significant niche both in industrial systems and residential heating installations.
Currently, you can purchase basic options like single-speed pumps without any control, as well as “smart” electronic pumps with pressure and flow control and multiple operating modes.
Despite all the advantages listed above, these pumps have one significant drawback — the quality of the water or heat carrier they work with. Regardless of the level of smart electronics involved, the core element of this type of pump equipment remains the mechanical part — the "wet rotor".
Since the rotor is washed by the pumped medium, its quality must be adequate — clean, and free from mechanical impurities (scale, sand, rust flakes, etc.).
The photo below shows a pump that was sent to us for servicing due to rotor jamming after just 1.5 months of operation.
The impeller and the gap between the rotor and stator were clogged with rust flakes, which caused the rotor to seize.
Conclusion — when using pumps of this type, it is crucial to ensure proper water treatment. With clean water, the pump will last well beyond the warranty period.
Otherwise, you should consider pump systems that are less sensitive to water quality — such as inline dry rotor pumps equipped with a standard asynchronous motor and mechanical seal.
June 17, 2025
Pumping carbon dioxide with a multi-stage pump
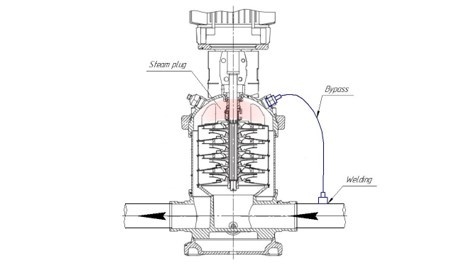
Carbon dioxide (CO₂) – a colorless gas (under normal conditions), easily soluble in water.
In addition to the widely known fact that it is an important element of the photosynthesis process, this substance is widely used in the food, pharmaceutical, agricultural, and mechanical engineering industries, among others.
In the technological process of carbon dioxide production, transportation means are essential, namely a pump unit. Carbon dioxide is in a liquid state at low temperature and high pressure.
In the photo below – a vertical multistage pump installed in the carbon dioxide production line. Frost (frozen water vapor contained in the air) is observed on the pump surface and shut-off valve .
The feature of this type of pumps is the ability to generate high pressure due to the number of impellers located on a single shaft one after another. This design allows achieving significant pressures (from 3 to 25 bar).
The disadvantage of vertical configuration is the danger of forming steam-air "plugs" in the upper part of the pump due to high liquid velocity and, consequently, local boiling of carbon dioxide.
It is in this part of the pump that the mechanical seal is located. This element prevents liquid leakage from the working chamber and should be cooled by the pumped liquid, but since a steam-air zone is formed where the seal operates without liquid – "dry running", the service life of the mechanical seal is significantly reduced.
In the case of "dry running", rapid wear of friction pairs and melting of rubber rings occurs.
To eliminate this problem, a bypass tube can be used. This pump piping element allows directing vapors to the suction line, thereby preventing the formation of a steam-air "pocket" in the mechanical seal area.
June 16, 2025
Manual barrel pumps
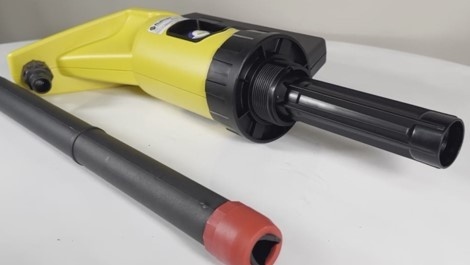
Manual barrel pumps are the optimal solution for small enterprises, car service stations, food production facilities—anytime there is a need for product dispensing or drawing a small amount of liquid for a specific technological process.
These pumps can be used for dispensing from large containers of automotive oil, vegetable oil, fertilizers, enzyme preparations, plant protection agents, antifreeze, glycol, alcohol, diesel fuel, gasoline, and more.
Our range of manual barrel pumps is represented by the Italian manufacturer FLUIMAC.
The “yellow” pump, model N-04, is designed for working with fuels, lubricants, and fat-based products.
The pump's construction is simple and reliable. The extendable rod allows use in containers of various depths, and the FKM rubber seal ensures chemical resistance and long service life.
The “blue” pump, model N-04 Blue, has a similar design, except it uses PTE rubber seals, allowing it to handle acid solutions, vinegar, adipic acid, and other chemically active substances.
The pump delivers 0.3 L per handle stroke, with a ¾ inch connection.
The telescopic suction tube is adjustable from 500 to 950 mm and has a diameter of 34 mm.
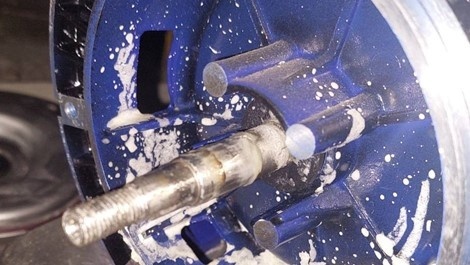
In general, for high-viscosity products, pump types such as impeller , lobe , gear , and diaphragm are commonly used — these are primarily positive displacement pumps.
For a number of products such as oil, transformer oil, a mixture of water and flour in a 1:4 ratio, beer wort, mash, and similar liquids, a centrifugal pump with an open or wide impeller can be successfully used.
An important aspect when using such a pump with the above-mentioned products is the need to rinse the pump chamber after the pumping process is complete.
This type of pump is equipped with a mechanical seal , which generally does not require maintenance during operation. However, if the pumped product is prone to crystallization, sticking, or clumping, this may cause damage to the seal.
The photo below shows damage to the rubber bellows of the mechanical seal.
This occurred due to a failure to rinse the pump chamber in time. As a result, the friction surfaces were "glued" together by a starchy mixture, and when the pump was restarted, the rubber bellows tore.
As a result, the product began to leak from the working chamber into the space between the pump support and the electric motor.
In this case, the operator noticed the leak in time, and the mechanical seal was replaced. Otherwise, prolonged leakage could have caused damage to the electric motor, leading to significantly higher repair costs and delays in the technological process.
Our company not only sells pumping equipment and spare parts but also provides qualified selection and maintenance recommendations.
June 10, 2025
Advantages and disadvantages of wet rotor pumps
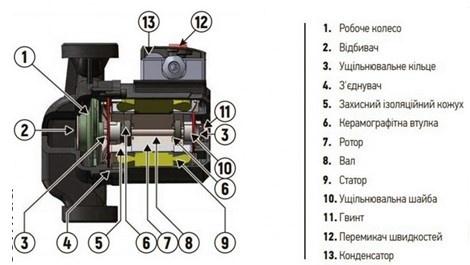
Pumps with a "wet rotor" have received their name due to the design feature – the pump rotor is supported by sliding bearings and is fully immersed in water.
The main advantage of this design is its noiseless operation. Since the rotor rotates on sliding bearings and lacks a cooling fan, the pump operates very quietly. Sometimes, the rotor's rotation can only be detected using a magnetic indicator.
Another advantage of this design is the absence of seals. It is a practically hermetic pump with only a vent plug at the end.
Moreover, most pumps with a "wet rotor" are equipped with a rotor speed switch, allowing optimal adjustment of the pump to your heating system even with minor calculation errors.
Undoubtedly, in private heating systems and in thermal nodes of multi-apartment buildings, where noise level is a critical factor, these pumps are virtually irreplaceable.
However, in industrial heating systems, boiler rooms, wood drying plants, and circulation cooling systems in the food industry, this design reveals its "downsides".
Since the gap between the rotor and stator is very small (0.5–2 mm depending on the model), the water cleanliness requirements are very high. Inclusions like scale, dirt, gasket remnants, or electrode fragments from pipe repairs or valve replacements can lead to pump failure.
This type of pump has low maintainability. Typically, service centers do not perform separate repairs of the rotor or stator or replace ceramic bearings. Instead, they offer complete replacement of the pump assembly, which costs about 80% of the pump's total price.
Another significant drawback, especially for industrial pumps, is the price. Many global leaders in pump equipment, such as Wilo, Grundfos, and DAB, have discontinued models with mechanical speed switching and now offer similar models with frequency control, which can be more than twice as expensive as the "old" models.
An alternative solution for replacing discontinued European-made pumps could be single-speed "wet rotor" pumps by EDWIN or using inline pumps with a "dry rotor" featuring a standard asynchronous motor.
June 6, 2025
Purchase of solar panels
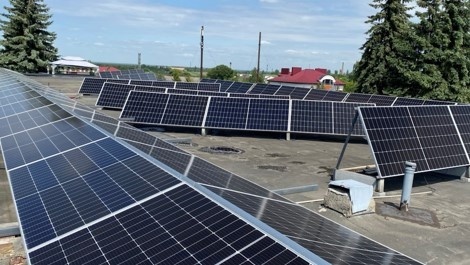
The first prototypes of solar panels were invented in the mid-19th century. Since then, they have been improved and gained popularity, but only in the past eight years have they seen massive adoption. Today, solar energy is not only a cost-effective investment but also an environmentally sound way to address ecological challenges. Solar panels reduce CO2 emissions, helping combat global warming and climate change.
Before purchasing solar panels, you need to determine the purpose: for resale or personal use. For example, if an individual installs a system to generate income, its capacity must not exceed 30 kW. For home energy supply, the system should match the consumption.
Panels vary in power and materials: monocrystalline (most common) and amorphous.
Let’s say you need 10 kW and choose 560 W panels.
Divide the total system capacity by the power of one panel.
Add 15–20% to compensate for potential losses.
10,000 W / 560 W = 17.8 panels
With 15–20% margin: 17.8 * 1.15 = 20.47 → round up to 21 panels.
So, to build a 10 kW system, you need 21 solar panels.
You can purchase these panels from us, by clicking this link .
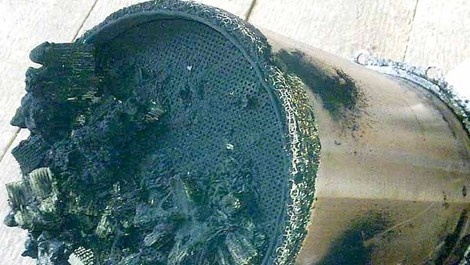
Particulate filters are one of the main components of a vehicle’s exhaust system. This device ensures the purification of exhaust gases from an internal combustion engine from solid particulate matter, known as soot, which forms during fuel combustion.
Modern automotive engines are equipped with automatic systems for filter regeneration, which operate without driver intervention. However, over time, this cleaning becomes insufficient, and the filter must be removed for cleaning at specialized facilities.
There are two main methods of cleaning particulate filters – chemical and hydrodynamic . The chemical method requires the use of special reagents and appropriate equipment.
In contrast, the hydrodynamic method is more cost-effective and environmentally friendly. It allows restoration of up to 98% of the filter’s capacity.
The main component of the hydrodynamic cleaning system is a centrifugal pump . Depending on the filter type, pumps with flow rates from 50 to 150 l/min and pressure of 4–7 bar are used.
The washing system can be of circulating or flow-through type. In circulating systems (where dirty water is filtered and reused), it is recommended to use single- or two-stage pumps with a pressure of 4–5 bar.
These pumps have an impeller wide enough to prevent clogging by soot and dirt particles.
In flow-through systems, vertical multistage high-pressure pumps (5–7 bar) can be used. The washing water does not return to the pump but is drained into the sewage, eliminating the risk of contamination.
Our specialists are always ready to assist you in the selection of pumping equipment for particulate filter cleaning stations.