Flow control of a positive displacement pump
Positive displacement pumps are devices that operate based on the principle of changing the volume of a working chamber. This can occur due to an eccentrically mounted impeller (in an impeller pump), rotation of gears, piston movement, membrane movement, change in hose volume (peristaltic pump), etc.
Given the operating principle of such a pump, it can be concluded that regulating its performance with shut-off valves (by closing valves on the discharge or suction line) may be harmful and dangerous both to the pump and the system in which it operates.
Unlike dynamic pumps, these pumps do not generate pressure but are capable of overcoming certain pressure, which may reach dozens or even hundreds of megapascals (MPa).
This means that if, for example, a gear pump is operating in a circulation system, the pressure gauge will actually show the resistance of the piping system (pipes, bends, filters).
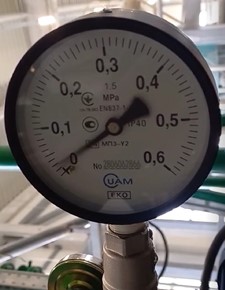
Pressure gauge in a transformer cooling system. A gear pump ENP 1010 is operating with a maximum pressure of 15 bar. The pressure gauge shows 0.2 bar.
Below in the photo – the result of closing the valve on the discharge pipe in the same system.
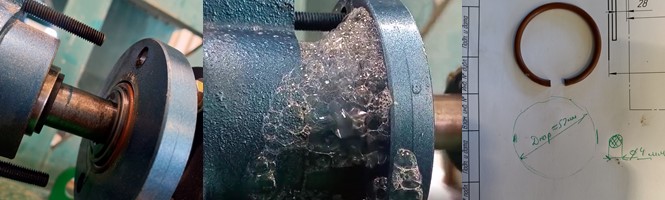
As a result of closing the valve, the sealing rubber was damaged.
Another example – an attempt to regulate flow with a valve in an impeller pump AlphaDynamic.
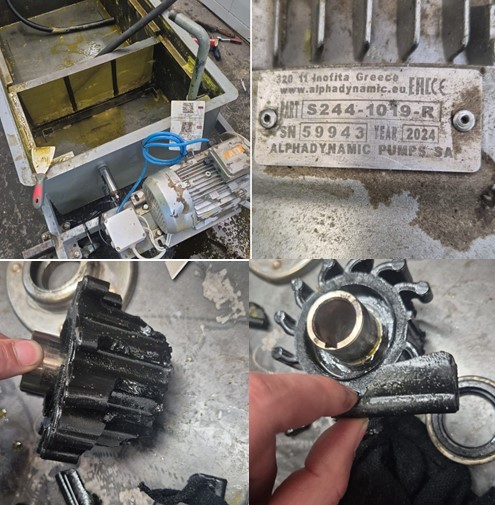
As a result – damage to the impeller and the need for repair.
Conclusion – the operation of a positive displacement pump should be regulated using a bypass line or frequency inverter. IT IS STRICTLY FORBIDDEN to close shut-off valves at the pump inlet or outlet. If a bypass line is not installed in the system, safety valves must be used.