- Home
- Engineering services and equipmentVacuum evaporation plant Decanter centrifuges, separatorsCrushers for grinding cereal crops in the process of feed, flour, ethanol productionControl and measuring instruments, sensors, flow meters for production automationDesign, construction of a distillery, distillationSpiral shell and tube heat exchangerIndustrial dryersSolid fuel boilersEnzymes, alcohol yeast, antiseptics for the production of alcoholEnergy auditSteam industrial boilers
- Enzymes, alcohol yeast, antiseptics for the production of alcohol
Enzymes, alcohol yeast, antiseptics for the production of alcohol
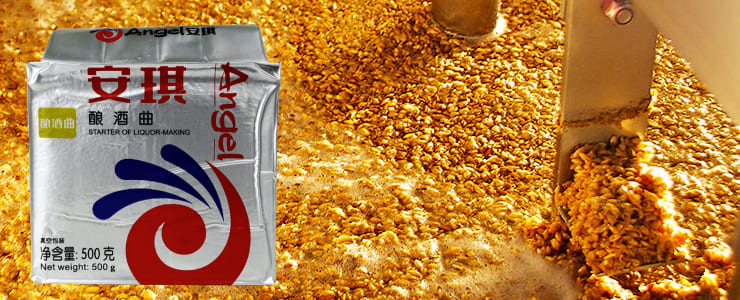
Alcohol, also known as ethyl alcohol, ethanol, or bioethanol, is a valuable substance for a number of industries, used as a solvent, raw material for pharmaceutical and cosmetic products, raw material for chemical enterprises, fuel additives, alcoholic beverage production, etc.
At the same time, the task arises of the most complete use of raw materials with the organization of complex and waste-free technologies for its processing. The problem of competitiveness and the creation of profitable production requires optimization not only as individual components of the production and commercial process, but also as a whole to fully use the resource potential of the enterprise.
For the production of ethanol from grain raw materials, enzyme preparations are used to convert grain starch into monosaccharides. The main enzyme preparations are alpha amylase and glucoamylase. Auxiliary enzyme preparations xylanase, beta-glucanase, protease.
Further, after enzymatic hydrolysis, the fermentation process (alcoholic fermentation) takes place with the help of yeast cells, as a result of which a brew containing ethanol is obtained 8-14 % Vol.
At all stages of the technological process, microbiological control is carried out in order to prevent the formation and reproduction of other microorganisms, except yeast cells.
To combat cantaminating microflora, antiseptic preparations containing antibiotics are used. These drugs prevent the formation and reproduction of other micro-organisms that use sugars for their development (necessary, in fact, for the production of ethanol) and harm the reproduction of yeast cells.
Optimal temperature | 32-34°С |
Total amount of yeast, billion/g | ≥ 6 |
Producer | Angel |
Humidity,% | ≤6,5 |
Operating temperature | 32-34°С |
Optimal temperature | 32-34°С |
Total amount of yeast, billion/g | ≥ 6 |
Producer | Angel |
Humidity,% | ≤6,5 |
Operating temperature | 32-34°С |
Optimal temperature | 32-34°С |
Total amount of yeast, billion/g | ≥ 6 |
Producer | Angel |
Humidity,% | ≤6,5 |
Operating temperature | 32-34°С |
Optimal temperature | 32-34°С |
Total amount of yeast, billion/g | ≥ 6 |
Producer | Angel |
Humidity,% | ≤6,5 |
Operating temperature | 32-34°С |
Optimal temperature | 32-34°С |
Total amount of yeast, billion/g | ≥ 6 |
Producer | Angel |
Humidity,% | ≤6,5 |
Operating temperature | 32-34°С |
Permissible ethanol content in the brew | ≤17% (V/V) |
Percentage of living yeast cells,% | ≥75 |
Total amount of yeast, billion/g | ≥ 25 |
Producer | Angel |
Humidity,% | ≤6,5 |
Optimal pH | 3.5-6.0 |
Optimal temperature | 32-34°С |
Permissible ethanol content in the brew | ≤ 23%(V/V) |
Percentage of living yeast cells,% | ≥80 |
Total amount of yeast, billion/g | ≥ 25 |
Optimal pH | 3.5-7.5 |
Operating pH | 3.5-7.5 |
Optimal temperature | 30-35°С |
Producer | Organika |
Operating temperature | 30-35°С |
Optimal pH | 3.8-4.5 |
Operating pH | 3.8-4.5 |
Optimal temperature | 32-35°С |
Producer | ERBSLÖH |
Operating temperature | 30-35°С |
Optimal pH | alpha-amylase - 5.5-6.5pH; glucoamylase - 4.0-4.5pH |
Optimal temperature | alpha-amylase - 85-95˚C; glucoamylase - 56-60˚С |
Enzyme | alpha-amylase, glucoamylase |
Producer | BTS Engineering |
Packaging | alpha-amylase - 50 ml, glucoamylase - 50 ml |
Optimal pH | alpha-amylase - 5.5-6.5pH; glucoamylase - 4.0-4.5pH |
Optimal temperature | alpha-amylase - 85-95˚C; glucoamylase - 56-60˚С |
Enzyme | alpha-amylase, glucoamylase |
Producer | BTS Engineering |
Packaging | alpha-amylase - 25 ml, glucoamylase - 25 ml |
Supply rate g/t | 150 |
Supply rate of grain | 90 |
Dosing, kg/t. of starch | 0,058-0,173 |
Optimal pH | 5.8-6.8 |
Operating pH | 5.0-8.5 |
Optimal pH | 3.5-7.5 |
Operating pH | 3.5-7.5 |
Optimal temperature | 30-35°С |
Producer | Organika |
Operating temperature | 30-35°С |
Optimal pH | 3.5-7.5 |
Operating pH | 3.5-7.5 |
Optimal temperature | 30-35°С |
Producer | TEGAFERM |
Operating temperature | 30-35°С |
Optimal pH | 3.5-7.5 |
Operating pH | 3.5-7.5 |
Optimal temperature | 30-35°С |
Producer | SternEnzym |
Operating temperature | 30-35°С |
Dosing, kg/t. of starch | 0,16-0,25 |
Optimal pH | 4.0-4.5 |
Activity, un/ml | 400,000 |
Operating pH | 3.0-5.0 |
Optimal temperature | 55-60°C |
Dosing, kg/t. of starch | 0,06-0,12 |
Optimal pH | 5.0-5.5 |
Activity, un/ml | 5,000 |
Operating pH | 4.0-7.0 |
Optimal temperature | 40-45°C |
Dosing, kg/t. of starch | 0,07-0,15 |
Optimal pH | 5.2-6.0 |
Activity, un/ml | 350,000 |
Operating pH | 5.0-8.0 |
Optimal temperature | 85-90°C |
Dosing, kg/t. of starch | 0,2-0,5 |
Optimal pH | 4.8-5.8 |
Activity, un/ml | 30,000 |
Operating pH | 4.0-7.0 |
Optimal temperature | 45-55°C |
Dosing, kg/t. of starch | 0,08-0,17 |
Optimal pH | 3.0-3.7 |
Activity, un/ml | 15,000 |
Operating pH | 2.0-5.0 |
Optimal temperature | 40-47°C |
Supply rate g/t | 80 |
Supply rate of grain | 48 |
Cost per TUK, UAH | 56,6 |
Dosing, kg/t. of starch | 0,029-0,086 |
Optimal pH | 5.8-6.8 |
Supply rate g/t | 400 |
Supply rate of grain | 240 |
Dosing, kg/t. of starch | 0,35-0,46 |
Optimal pH | 3,6-5,5 |
Operating pH | 3,6-5,5 |
Dosing, kg/t. of starch | 0,4-1,8 |
Optimal pH | 4,0-6,0 |
Operating pH | 4,0-6,0 |
Optimal temperature | 30-70°С |
Enzyme | complex of enzymes |
Dosing, kg/t. of starch | 0,1-0,25 |
Optimal pH | 4,5 -6,0 |
Operating pH | 4,5 -6,0 |
Optimal temperature | 85-92°С |
Enzyme | alpha-amylase |
Dosing, kg/t. of starch | 0,058-0,28 |
Optimal pH | 3,5-6,0 |
Operating pH | 3,5-6,0 |
Optimal temperature | 28-37°С |
Enzyme | protease |
Dosing, kg/t. of starch | 0,36-0,9 |
Optimal pH | 3,0-6,0 |
Operating pH | 3,0-6,0 |
Optimal temperature | 30-75°С |
Enzyme | glucoamylase |
Dosing, kg/t. of starch | 0,19-0,62 |
Optimal pH | 4,5 -7,0 |
Operating pH | 4,5 -7,0 |
Optimal temperature | 50-95°С |
Enzyme | alpha-amylase |
Producer | BTS Engineering |
Producer | BTS Engineering |