- Home
- Engineering services and equipmentVacuum evaporation plant Decanter centrifuges, separatorsCrushers for grinding cereal crops in the process of feed, flour, ethanol productionControl and measuring instruments, sensors, flow meters for production automationDesign, construction of a distillery, distillationSpiral shell and tube heat exchangerIndustrial dryersSolid fuel boilersEnzymes, alcohol yeast, antiseptics for the production of alcoholEnergy auditSteam industrial boilers
- Solid fuel boilers
- Combined solid fuel boilers Retra-4M
Combined solid fuel boilers Retra-4M
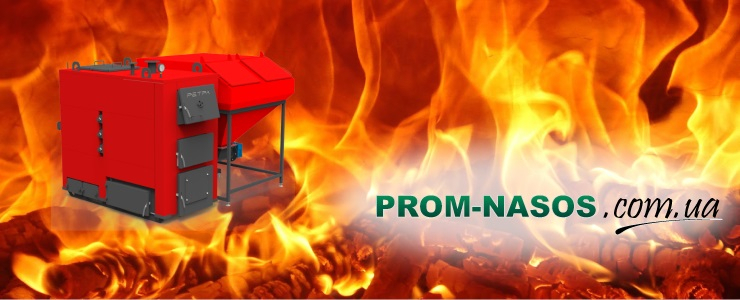
Power from 25 to 2000 kW!
Solid fuel boiler Retra-4M is a structure made of solid sheet steel, a boiler with a system of automated fuel supply.
Works in two modes:
- Manual fuel supply (wood, coal, briquette, etc.). Fuel is loaded through a special hatch. The process of efficient combustion of fuel in the furnace occurs due to the intensive supply of air around the perimeter of the camera. This forms an "air cocoon" around the fuel. Gas did not burn out in the firebox due to lack of air burns out due to the supply of secondary air, ensuring a high efficiency.
- Automatic fuel supply (pellets, coal with a fraction of up to 15 mm, chips, husks). Fuel loading carried out automatically from the hopper by a screw auger (driven by a geared motor) to the pellet burners. The most efficient combustion of fuel in a pellet burner is due to the blowing of air fan. The operation of the screw conveyor and fan is controlled by a microprocessor-based thermostat.
Design features
- There are two furnaces - the upper one for burning large-sized raw materials and the lower one for burning small fuels using a retort (pellet) burner;
- robot in manual and automatic mode;
- the increase in the volume of the bunker will provide without interruption to the boiler robot up to 3-5 dB;
- double protection against fires in the feed screw.
The principle of operation of automation
During and after the automatic loading of the necessary portion of fuel to the burner, the fan intensively pumps air to achieve a stable combustion temperature. This cycle is repeated until the temperature of the water in the boiler rises to the set thermostat base values. After that, the automation goes into combustion mode. When the temperature drops to the specified minimum level (recommended: 40-45 °С), the automatic loading of fuel from hopper and turning on the fan and the boiler operation cycle is repeated.
If the temperature reaches the set maximum level (recommended: 85-90 °C), automatic cuts off the fuel supply and the fan goes into the support state.
Also, the thermostat is able to control the operation of the central heating pump in accordance with the set parameters.