- Home
- Mechanical sealsMechanical seals by typeMechanical seal for the pumpMechanical seals by brandShaft runout seal for agitators, hoppers and conveyorsRepair of mechanical seals, friction pairsManufacturing of cuffs, rings, oil sealsManufacturing of parts from silicon carbide, zirconium silicateInsulator bearing protection Bearing defender isolator
- Repair of mechanical seals, friction pairs
Repair of mechanical seals, friction pairs
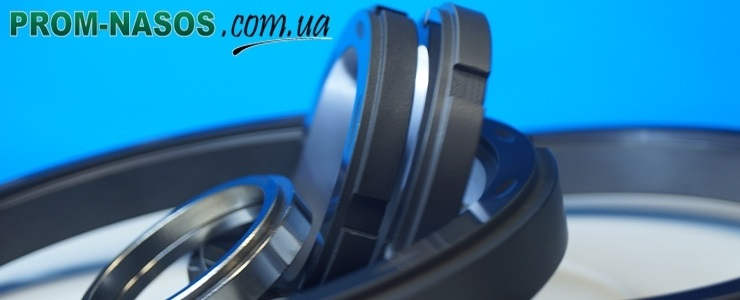
- Manufacturing of friction pairs for mechanical seals according to the customer's technical specification.
- Development of technical specifications, justification of materials of friction pairs according to structures.
To order mechanical seal parts, send us an email drawing of the part, or a sample of a worn seal part, friction or slip pairs.
Carbon graphite materials for mechanical seal rings are divided into annealed and graphite. The composition of both is approximately the same, and they differ only in the degree of heat treatment. Coke, soot, graphite and fuel and energy complex are used as starting materials in the production of carbon graphite. After the final pressing, the workpieces are fired in a furnace and fired carbon graphite materials are obtained. If, after firing, exposure is also used in a furnace with a temperature of 2400-2600 °C, at which part of the amorphous coal turns into graphite, then such materials are called graphite. At the same time, the thermal conductivity of carbon graphite increases (approximately 2 times), their antifriction properties improve, oxidation resistance increases, but strength decreases. After firing and graphitization, carbon graphite materials have a porosity of 6-30%. To eliminate it, improve the antifriction and mechanical properties of carbon graphite, they are impregnated with resins, salts, metals, etc. In general, impregnation reduces porosity, increases the modulus of elasticity, hardness, temperature coefficient of linear expansion and thermal conductivity of the material.
Carbon-based antifriction materials are divided into the following main types:
- carbon annealed with impregnation;
- graphite impregnated;
- graphit-fluoroplast;
- silicified graphite.
The wide range of physical and mechanical properties of carbon materials is due to the variety of component compositions and production methods. Graphite 2P-1000 impregnated with phenol-formaldehyde resin and graphite at-1500 and AG-1500 impregnated with lead or Babbit are widely used in the construction of mechanical seals. Impregnation of porous graphite with resins, salts, metals, in particular lead, tin, copper, antimony, is usually carried out in autoclaves, where at temperatures above the melting point of the impregnation material, pressure and vacuum are created alternately to fill the voids in the graphite body with the impregnation material.
One of the most commonly used carbon graphite materials is silicified graphite. It consists of hard grains of silicon carbide interspersed with softer inclusions of silicon and carbon. The high wear resistance and durability of silicified graphite is due to the special structure of the material, which is a rigid frame made of high-hardness silicon carbide and free graphite included in it, which provides high antifriction properties and thermal conductivity.
For mechanical seals, Silicated Graphite of several grades is used: SG-t, SG-P (they differ in the ratio of components and have different production technologies) and Gakk 30/63, Gakk 60/25, Gakk 55/40 (aluminum-carbon silicon graphite designed specifically for friction pairs of mechanical seals). These materials work in pairs of friction separately or in combinations with each other. Silicified graphite is obtained by impregnating the initial graphite over the entire volume with liquid silicon at temperatures above 2000 °C.
In this case, the reaction occurs to form silicon carbide. However, in a chemical reaction, not all silicon is bound to carbon - free silicon in silicified graphite limits the chemical stability of these materials.
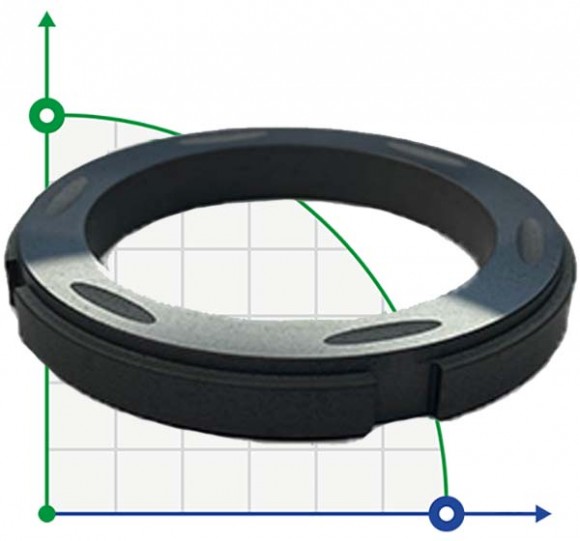
In particular, silicified graphite G-T and SG-P are unstable in alkalis. Silicified Graphite Gakk 55/40 is more stable under these conditions and is currently the most versatile antifriction material with high chemical resistance. Friction units made of silicified graphite work at temperatures up to 350 °C. products made of silicated graphite are resistant to aggressive media: hydrochloric, acetic, phosphoric, sulfuric, nitric, formic, hydrofluoric acids, caprolactam melt, methyl chloride, ethyl acetate and acetic anhydride.
In the last decade, silicon carbide materials, such as SILKAR, ROCAR, etc., have been widely used in mechanical seal units. SILKAR silicon carbide contains significantly more silicon carbide and less carbon by weight compared to silicified graphite. It has significantly higher strength, modulus of elasticity and coefficient of thermal conductivity; its wear resistance is 2-3 times higher than that of SG-P. ROCAR®s silicon carbide (0.98% sic, 0.1% Free C, 0.09% A1, 0.014% Ti, 0.028% Fe, 0.006% CA; graphite - other) produced in the Czech Republic (reaction-sintered silicon carbide) is characterized by high performance characteristics: erosion, thermal and chemical resistance, reliability and durability, durability.
Manufacturers use silicon carbide and silicified Graphite of two grades as friction pairs: solid, which is practically a monolith of silicon carbide; modified (or Cork), which is obtained by the action of a Silicon pair on a carbon ring of a given configuration. The silicification process goes to a shallow depth (0.5-1 mm), while the ring remains porous and must be impregnated.
According to the company "Burgmann" (Germany), silicon carbide exhibits high chemical resistance in various media and, above all, in mineral acids: hydrochloric, nitric, sulfuric, phosphoric and hydrogen fluoride (without impurities)-at different concentrations and temperatures. Silicon carbide is characterized by high chemical stability, thermal conductivity and wear resistance. The disadvantage is low tensile strength and brittleness. One of the disadvantages of carbon-based antifriction materials is the low impact strength, but this is manifested only at the stage of processing the part and installing the seal; during the operation of the mechanical seal, the impact axial loads are damped by the elastic element.
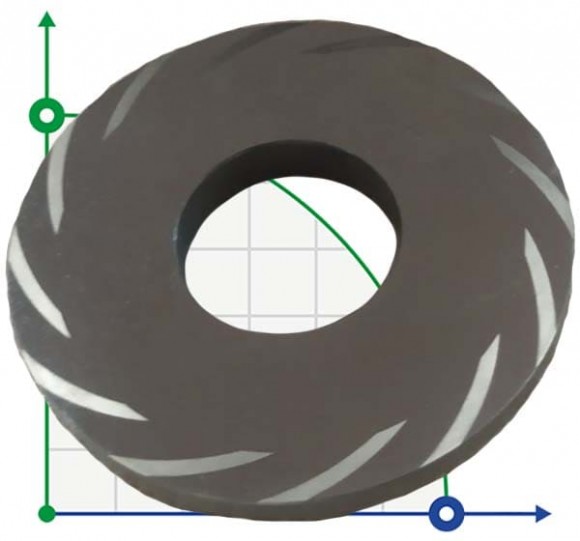
Tungsten carbide-based alloys are often used in friction pairs of mechanical seals. Cobalt and nickel are most often used as a bond for sintering tungsten carbides. Tungsten carbide gives the alloy hardness, compressive strength, hardness, wear resistance, and bond metal - impact strength and flexural strength. Tungsten carbide with cobalt as a bond has limited application, mainly for abrasive-containing media. Cobalt has a low chemical resistance-it dissolves even in distilled water, so it can not be used in food processing devices. Cobalt, which has a long Half-Life, should not be used in seals of nuclear power plant pumps [9]. The cobalt bundle of tungsten carbide Rings is subject to severe corrosion in seawater. If nickel is used instead of a cobalt bond, then such phenomena do not occur. Due to the low temperature coefficient of linear expansion of hard alloys (2-3 times less than corrosion-resistant steel), the deformation of friction surfaces is insignificant.
The high thermal conductivity of hard alloys (only silicified graphite and graphite coalgraphites have higher thermal conductivity) makes it possible to use them under conditions of high thermal loads.
The exclusivity of ceramics is determined by its chemical stability in environments with strong oxidizing properties, in which other materials are unstable, for example, in Oleum. Mineral ceramics are made on the basis of aluminum oxide. Thus, mineral ceramics CM-332, containing 99% aluminum oxide (corundum), has high resistance in environments with strong oxidizing properties. Due to its brittleness and relatively low thermal conductivity, ceramics are subject to thermal cracking during sharp cooling and rapid heating, so the "lubrication starvation" mode for ceramics is undesirable. In domestic mechanical seal designs, CM-332 mineral ceramics are used in conjunction with graphite-fluoroplast F4K20.
Producer | BTS Engineering |
Material | Sic |
Country of Origin | China |
Application | KSB |
Shaft diameter | 70 |
Producer | BTS Engineering |
Material | TC/VITON |
Application | Borger |
Producer | BTS Engineering |
Material | Sic |
Country of Origin | China |
Application | KSB |
Producer | BTS Engineering |
Material | Sic |
Pressure | 5,5 МПа |
Operating temperature | +25°C |
Application | Sulzer MSD |
Producer | BTS Engineering |
Material | Sic-C-Si |
Pressure | 5,5 МПа |
Operating temperature | +25°C |
Application | Sulzer MSD |
Producer | BTS Engineering |
Material | Sic |
Pressure | 2.5 MPa |
Operating temperature | -33°C + 41°C |
Application | Worthington ERP |
Producer | BTS Engineering |
Material | Sic-C-Si |
Pressure | 2.5 MPa |
Operating temperature | -33°C + 41°C |
Application | Worthington ERP |
Producer | BTS Engineering |
Material | CAR |
Application | Sefco C-20 |
Producer | BTS Engineering |
Material | Sic |
Application | Sefco C-20 |
Producer | BTS Engineering |
Material | Sic |
Pressure | 2 MPa |
Operating temperature | -25°C +220°C |
Rotation velocity | 20 m/s |
Producer | BTS Engineering |
Material | Sic |
Pressure | 2 MPa |
Operating temperature | -25°C +220°C |
Rotation velocity | 20 m/s |